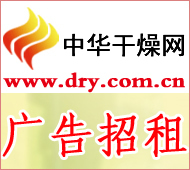
China Drying Network News On September 5, Liaoyang Petrochemical successfully completed a series of R&D operations such as scorching, chlorination, reduction, and sulfidation of PAI-01 catalysts, and successfully regenerated the domestically produced catalysts in the PetroChina system for the first time.
The regeneration of this catalyst has achieved remarkable results. It has increased the conversion rate of ethylbenzene in the 250,000-ton/year paraxylene plant of Liaoyang Petrochemical by 5%, and the production of paraxylene by 1.5 tons/hour.
According to reports, the PAI-01 isomerization catalyst is an ethylbenzene conversion catalyst independently developed by PetroChina. It was first used in the 250,000 tonne/year paraxylene plant of Liaoyang Petrochemical Corporation in 2009. It has been operating for 3 years continuously, and its activity and choice Sexuality has declined. In order to increase the activity of the catalyst, reduce the operating cost, increase the conversion of ethylbenzene and the production of p-xylene, the technical force of Liaoyang Petrochemical Company will scorch and regenerate the catalyst. Under the guidance of technical experts of the China Petroleum and Petrochemical Research Institute, the key links such as temperature difference, temperature increase rate, and oxygen content control at the reactor entrance during regenerative scrambling were repeatedly demonstrated, and a scientific regeneration program was formulated, and the PAI- Type 1 isomerization catalyst regeneration.
1.MAIN APPLICATION
Pharmaceutical industry: tablet granule, granule granule, capsule granule
Food industry: cocoa, coffee, milk powder, granular juice, condiments and so on
Other industries: pesticide, chemical fertilizer, feed, pigment, dye chemical industry, powder or granular wet material drying
Coating industry: pellet, outer protective layer, color preparation, slow release, film, enteric coating, etc
2.FEATURES
Through powder granulation, improve fluidity and reduce dust flying
Through powder granulation, its solubility can be improved
Mixing - Granulating - drying - in one machine (one-step granulating)
Using antistatic filter material, safe operation of equipment
Pressure relief hole, once explosion, equipment personnel will not be hurt
The equipment has no dead Angle, easy loading and unloading, clean and meet GMP standards
3.WORKING PRINCIPLE
Material powder particles, in the raw material container (fluidized bed) in a circular fluidization state, by the purification of the heated air preheating and mixing, the adhesive solution emulsified into the spray, so that a number of particles aggregated into aggregates containing adhesive. Due to the continuous drying of the material by hot air, the water in the aggregates evaporates and the adhesive solidifies. This process is repeated to form the ideal uniform spherical particles with multiple micropores
In addition we also have other machines for u chosoe,such as spices Powder Pulverizer ,powder mixer,Capsule Filling Machine,capsule Polishing Machine,Capsule Counting Machine,tablet press,vacuum dryer etc
Cinnamon Powder Fluidized Granulating Dryer,Fish Feed Fluidized Granulating Dryer,Thin Film Fluidized Granulating Dryer,Easy Cleaning Fluidized Granulating Dryer,New Arrival Fluidized Granulating Drye
Jiangyin yongchang medicine machinery co,.ltd , https://www.jyycgrinderline.com