Model NO.: plastic injection mould Mhs-142
Runner: Hot Runner
Design Software: UG
Installation: Fixed
Certification: TS16949, CE, ISO, FDA
Standard: DME
Customized: Customized
Product Name: Plastic Injection Mould Mhs-142
Mould Matieral: Different Grade: P20, S136, 2316, H13, etc.
Surface Treatment: Mirror Polish, Polish, Texture
Quality: ISO9001:2000 Certified
Mould Base: Lkm, Dme, Hasco etc ;
Steel Hardness: 20-60HRC
Treatment: Pre-Harden, Nitride, Heat Treatment, Quenching
Mould Life: 50K - 1 Million Cycles
Product Design Software: Ug, CAD, PRO-E, Solid Works etc
Payment: L/C, T/T, D/P, etc
Trademark: Minghuasheng
Transport Package: Crate/Pallet
Specification: 1000T double injection
Origin: Guangdong, China
HS Code: 8480719090
Model NO.: plastic injection mould Mhs-142
Runner: Hot Runner
Design Software: UG
Installation: Fixed
Certification: TS16949, CE, ISO, FDA
Standard: DME
Customized: Customized
Product Name: Plastic Injection Mould Mhs-142
Mould Matieral: Different Grade: P20, S136, 2316, H13, etc.
Surface Treatment: Mirror Polish, Polish, Texture
Quality: ISO9001:2000 Certified
Mould Base: Lkm, Dme, Hasco etc ;
Steel Hardness: 20-60HRC
Treatment: Pre-Harden, Nitride, Heat Treatment, Quenching
Mould Life: 50K - 1 Million Cycles
Product Design Software: Ug, CAD, PRO-E, Solid Works etc
Payment: L/C, T/T, D/P, etc
Trademark: Minghuasheng
Transport Package: Crate/Pallet
Specification: 1000T double injection
Origin: Guangdong, China
HS Code: 8480719090
Custom Precision plastic  Injection used mould for auto parts
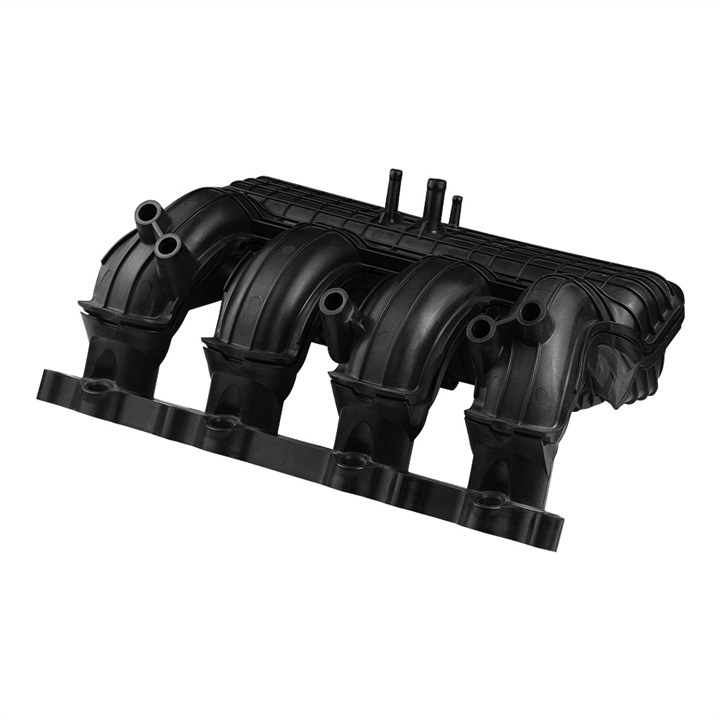
Â
Plastic Injection Molding Description:Â 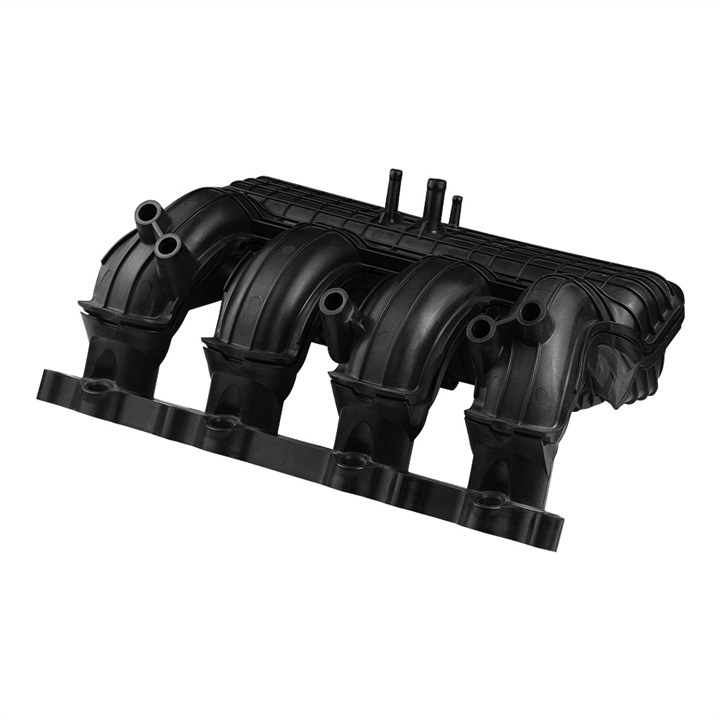
Â
Product name | plastic injection mould Mhs-142 |
Plastic Parts Material | ABS, PBT, PC, PMMA, POM, PP, PPS, PVC, TPE, TPO, TPU, etc |
Mold Standard | DME, LKM, HASCO, etc |
Runner | Hot or Cold |
Injection Machine | 100T-1600T |
Cycle time | 10-120 seconds |
Process | CNC, high speed carve, EDM, wiring-cutting, drill, Polish etc |
Gate | Submarine gate, tunnel gate, side/edge gate, direct gate, pin point gate, sprue gate, diaphragm gate, fan gate, cashew gate, hook gate, hot tip, hot drop, valve gate etc. |
Product Design Software | UG, CAD, PRO-E, Solid Works etc |
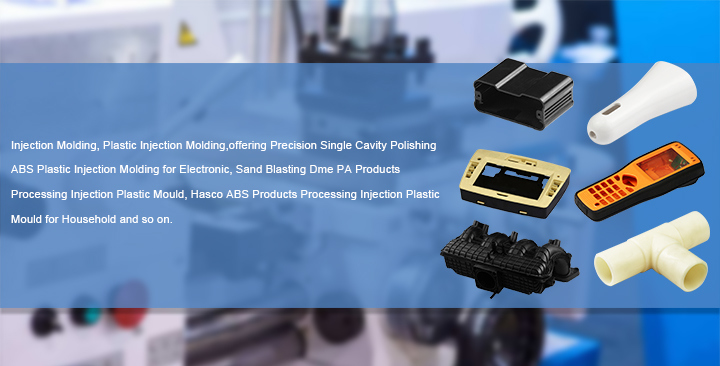
Product Process:Â
1. Mold Design Control
2. Mold Steel Hardness Inspection
3. Mold Electrodes Inspection
4. Mold Core and Cavity Steel Dimension Inspection
5. Mold Pre-Assembly Inspection
6. Mold Trial Report and Samples Inspection
7. Pre-Shipment Final Inspection
8. Export Product Package InspectionÂ

Application for Car; Household Appliances; Furniture; Commodity; Electronic; Home Use; Hardware; etc
Design Definition Requirements:Â
1 Mold basic info sample;Â
2 Plastic components function;Â
3 2D drawin( weight) or, 3D drawing;Â
4 Quantity or technical requirements;Â
5 Annually forecast or MFQ;Â
6. Surface treatment requirements, sample is better;Â
7 Other keypoint
Business Description:Â
We can OEM or ODM for your new project:Â
Injection Plastic Mold, Prototype mold and Mold insert
Stamping mold and parts
Precision machining
Auto mold and parts
Household mold and parts
Medical mold and parts
Our Advantage:Â
1. Offering competitive price;Â
2. Strong design and engineering ability;Â
3. Advanced production technoIogy and equipment;Â
4. Strict quality controI system;Â
5. Team-work with customer;Â
6. Flexible management and excellence service;Â
7 Good After-sale service.Â
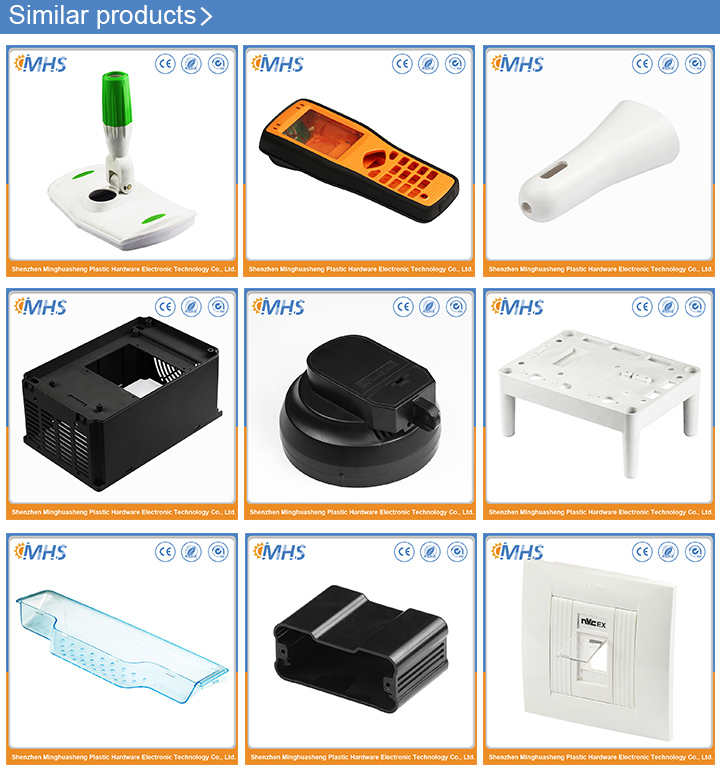
Product Packing:Â
Product weight: 5.0g~15kgs
Shipping Packaging: Wooden case or according to customer's requirement
Lead time: 2-8 weeks
Our company:Â
Shenzhen Ming Hua Sheng plastic hardware electronic technology Co., Ltd locates in Pinghu Shenzhen China. We offer manufacturing service including mold design and fabricating, molding/casting, CNC machining and rapid prototyping, Injection molding process business. We are also ready to serve to our customer with engineering support whenever needed. Also we are very happy to support our customer who has amazing and inspiring new idea, we can offer excellent support for the startup project.Â
Our services involved in telecommunication, automotive, consumer electronic, medical, home appliance, and industrial component etc.Â
Our constant focus is on delivery of the highest quality product and service at the best price, we can take a product from concept to production quickly, efficiently, and cost effectively. Currently we are having shipping to customers throughout North America, Europe, Australia, MID-east and India etc.Â
The company humanized management system for the implementation of standards. Abiding by the "implementation of the management, improve the efficiency, quality first, customer satisfaction" business philosophy, persevere for customers with high quality and high efficiency service. "Is the credibility of the quality assurance, to meet customer demand, the essence of" sincere service is to provide quality service to our customers permanent Connaught principle to provide our customers welcome customers patronage!Â
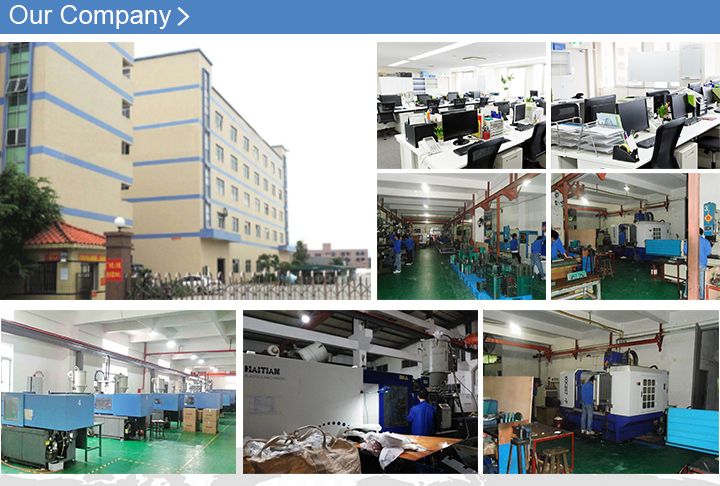
FAQ:Â
1. Q: I have an idea for a new product, but I don't know if it can be manufactured. Can you help?Â
A: Yes! We are always happy to work with potential customers to evaluate the technical feasibility of your idea or design and we can advise on materials, tooling and likely set-up costs.Â
2. Q: What are the advantages to have my parts manufactured locally?Â
A: We can offer quick reaction times to any changes in specification, batch size or material. We can ship small or large quantities anywhere in North America, Europe overnight to accommodate unforeseen changes in demand.Â
3. Q: My components have already been developed on CAD. Can you use the drawings?Â
A: Yes! DWG, DXF, IGES, Solid works and STP, X_T files can all be used to generate quotes, models and mould tools -Â this can save time and money in producing your parts.Â
4. Q: Can IÂ test my idea/component before committing to mould tool manufacture?Â
A: Yes, we can use CAD drawings to make Prototype models for design and functional evaluations or market test.Â
5. Q: What type of plastic is best for my design/component?Â
A: Materials selection depends on the application of your design and the environment in which it will function. WÂ e will be happy to discuss the alternatives and suggest the best material.Â
6. Q: What type of mould tool do IÂ need?Â
A: Mould tools can be either single cavity (one part at a time) or multi-cavity (2, 4, 8 or 16 parts at a time). Single cavity tools are generally used for small quantities, up to 10, 000 parts per year whereas multi-cavity tools are for larger quantities. We can look at your projected annual requirements and recommend the best tooling option for you.Â
7. Q: Ok, I've decided to go ahead with my project. How long will it take to get my parts?Â
A: It can take 3Â to 6Â weeks to have the mould tool manufactured depending on the part's complexity, size and the number of impressions/ cavities (single or multiple). After we receive your final approval on the tool preliminary design, you can expect delivery of T1 parts within 3-6 weeks. And during mold building process, mold build Weekly Update will be provided to you every week for your better understanding of the manufacturing progress in our work shop.Â
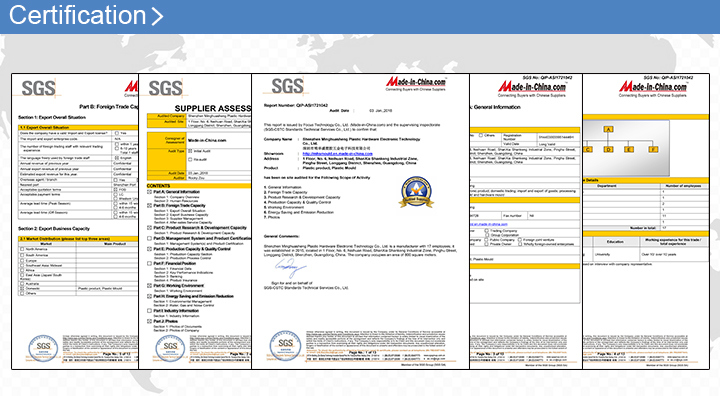
Â
Custom Precision plastic  Injection used mould for auto parts
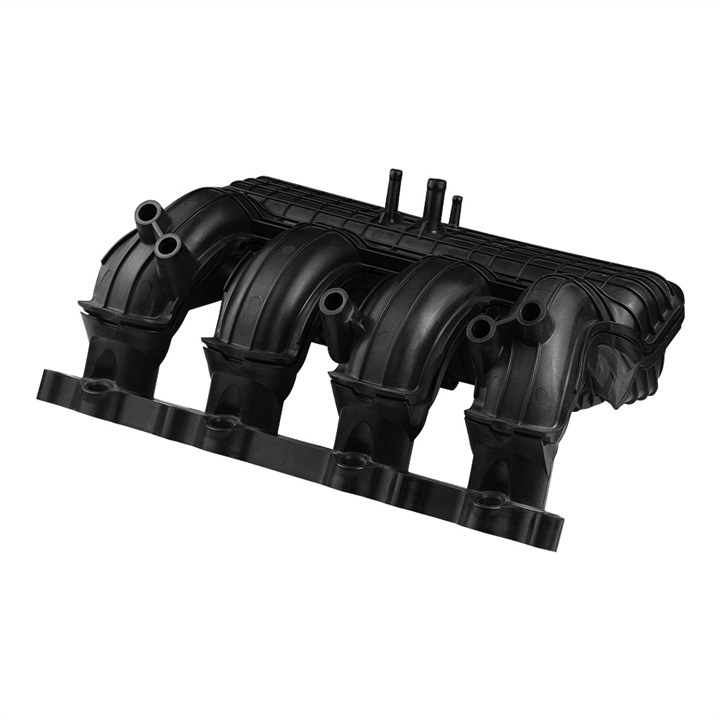
Â
Plastic Injection Molding Description:Â 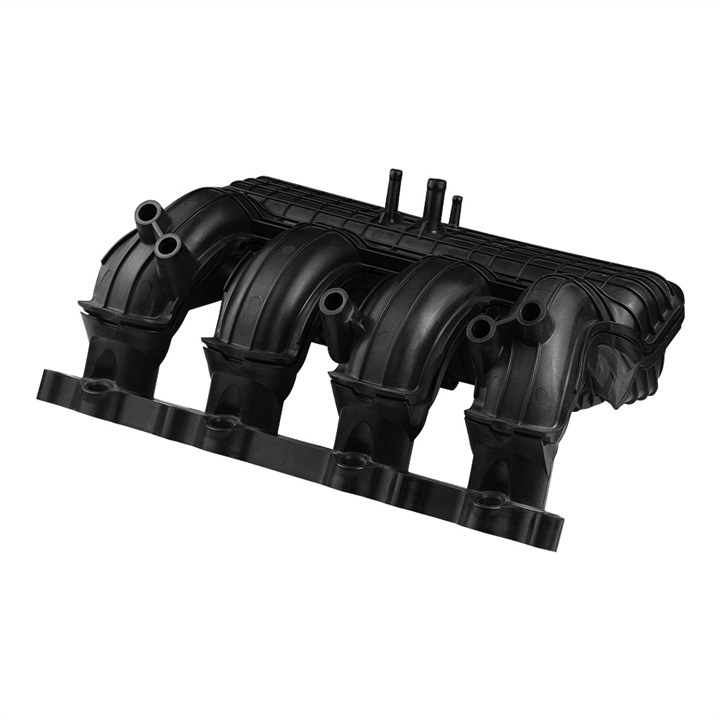
Â
Product name | plastic injection mould Mhs-142 |
Plastic Parts Material | ABS, PBT, PC, PMMA, POM, PP, PPS, PVC, TPE, TPO, TPU, etc |
Mold Standard | DME, LKM, HASCO, etc |
Runner | Hot or Cold |
Injection Machine | 100T-1600T |
Cycle time | 10-120 seconds |
Process | CNC, high speed carve, EDM, wiring-cutting, drill, Polish etc |
Gate | Submarine gate, tunnel gate, side/edge gate, direct gate, pin point gate, sprue gate, diaphragm gate, fan gate, cashew gate, hook gate, hot tip, hot drop, valve gate etc. |
Product Design Software | UG, CAD, PRO-E, Solid Works etc |
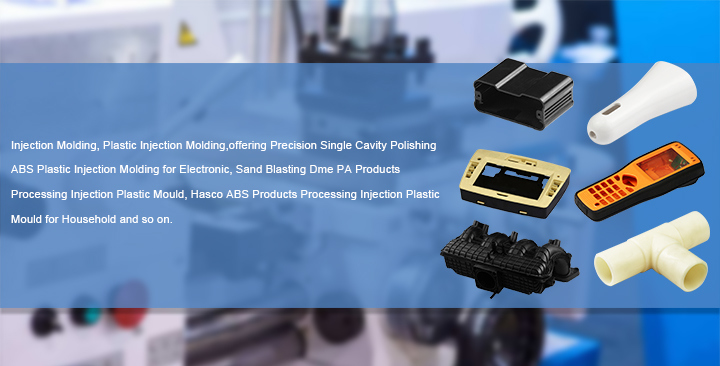
Product Process:Â
1. Mold Design Control
2. Mold Steel Hardness Inspection
3. Mold Electrodes Inspection
4. Mold Core and Cavity Steel Dimension Inspection
5. Mold Pre-Assembly Inspection
6. Mold Trial Report and Samples Inspection
7. Pre-Shipment Final Inspection
8. Export Product Package InspectionÂ

Application for Car; Household Appliances; Furniture; Commodity; Electronic; Home Use; Hardware; etc
Design Definition Requirements:Â
1 Mold basic info sample;Â
2 Plastic components function;Â
3 2D drawin( weight) or, 3D drawing;Â
4 Quantity or technical requirements;Â
5 Annually forecast or MFQ;Â
6. Surface treatment requirements, sample is better;Â
7 Other keypoint
Business Description:Â
We can OEM or ODM for your new project:Â
Injection Plastic Mold, Prototype mold and Mold insert
Stamping mold and parts
Precision machining
Auto mold and parts
Household mold and parts
Medical mold and parts
Our Advantage:Â
1. Offering competitive price;Â
2. Strong design and engineering ability;Â
3. Advanced production technoIogy and equipment;Â
4. Strict quality controI system;Â
5. Team-work with customer;Â
6. Flexible management and excellence service;Â
7 Good After-sale service.Â
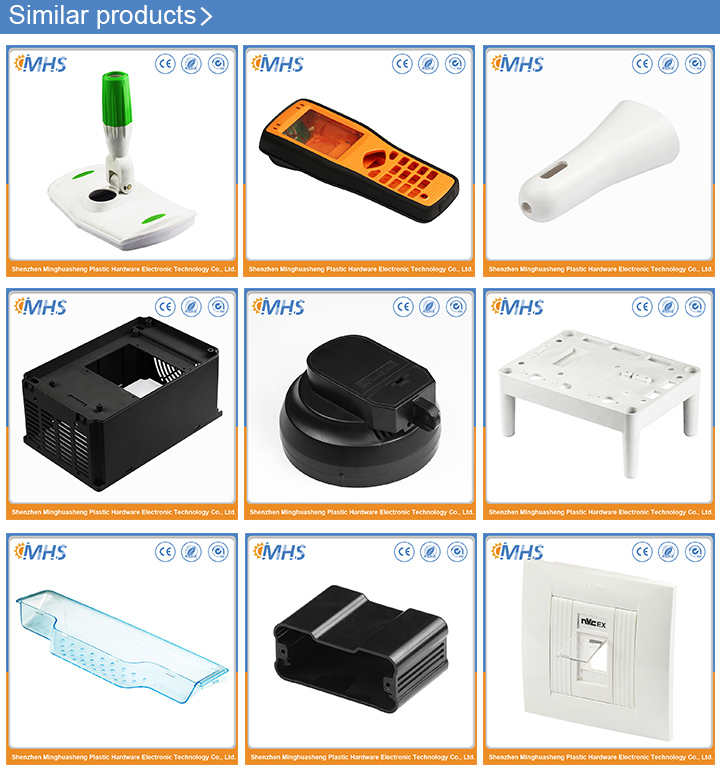
Product Packing:Â
Product weight: 5.0g~15kgs
Shipping Packaging: Wooden case or according to customer's requirement
Lead time: 2-8 weeks
Our company:Â
Shenzhen Ming Hua Sheng plastic hardware electronic technology Co., Ltd locates in Pinghu Shenzhen China. We offer manufacturing service including mold design and fabricating, molding/casting, CNC machining and rapid prototyping, Injection molding process business. We are also ready to serve to our customer with engineering support whenever needed. Also we are very happy to support our customer who has amazing and inspiring new idea, we can offer excellent support for the startup project.Â
Our services involved in telecommunication, automotive, consumer electronic, medical, home appliance, and industrial component etc.Â
Our constant focus is on delivery of the highest quality product and service at the best price, we can take a product from concept to production quickly, efficiently, and cost effectively. Currently we are having shipping to customers throughout North America, Europe, Australia, MID-east and India etc.Â
The company humanized management system for the implementation of standards. Abiding by the "implementation of the management, improve the efficiency, quality first, customer satisfaction" business philosophy, persevere for customers with high quality and high efficiency service. "Is the credibility of the quality assurance, to meet customer demand, the essence of" sincere service is to provide quality service to our customers permanent Connaught principle to provide our customers welcome customers patronage!Â
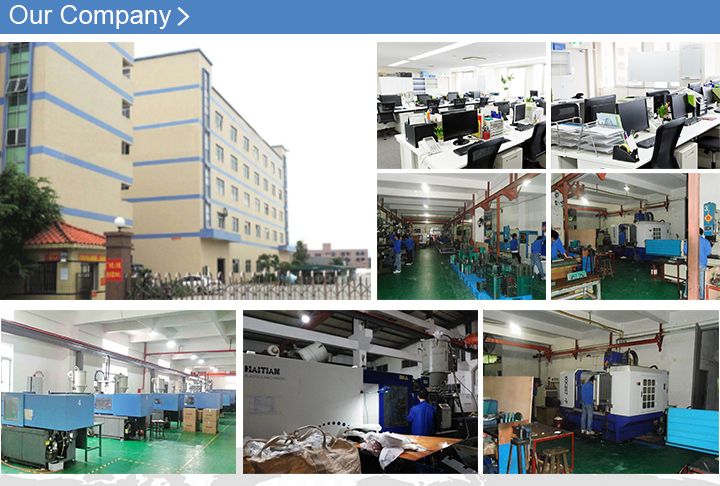
FAQ:Â
1. Q: I have an idea for a new product, but I don't know if it can be manufactured. Can you help?Â
A: Yes! We are always happy to work with potential customers to evaluate the technical feasibility of your idea or design and we can advise on materials, tooling and likely set-up costs.Â
2. Q: What are the advantages to have my parts manufactured locally?Â
A: We can offer quick reaction times to any changes in specification, batch size or material. We can ship small or large quantities anywhere in North America, Europe overnight to accommodate unforeseen changes in demand.Â
3. Q: My components have already been developed on CAD. Can you use the drawings?Â
A: Yes! DWG, DXF, IGES, Solid works and STP, X_T files can all be used to generate quotes, models and mould tools -Â this can save time and money in producing your parts.Â
4. Q: Can IÂ test my idea/component before committing to mould tool manufacture?Â
A: Yes, we can use CAD drawings to make Prototype models for design and functional evaluations or market test.Â
5. Q: What type of plastic is best for my design/component?Â
A: Materials selection depends on the application of your design and the environment in which it will function. WÂ e will be happy to discuss the alternatives and suggest the best material.Â
6. Q: What type of mould tool do IÂ need?Â
A: Mould tools can be either single cavity (one part at a time) or multi-cavity (2, 4, 8 or 16 parts at a time). Single cavity tools are generally used for small quantities, up to 10, 000 parts per year whereas multi-cavity tools are for larger quantities. We can look at your projected annual requirements and recommend the best tooling option for you.Â
7. Q: Ok, I've decided to go ahead with my project. How long will it take to get my parts?Â
A: It can take 3Â to 6Â weeks to have the mould tool manufactured depending on the part's complexity, size and the number of impressions/ cavities (single or multiple). After we receive your final approval on the tool preliminary design, you can expect delivery of T1 parts within 3-6 weeks. And during mold building process, mold build Weekly Update will be provided to you every week for your better understanding of the manufacturing progress in our work shop.Â
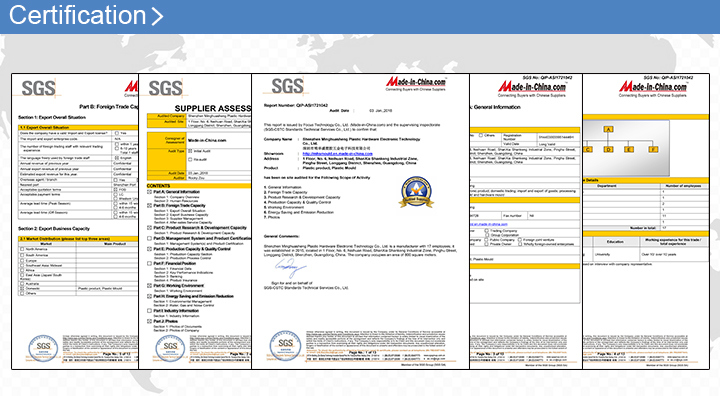
Â
Tubular Condenser,Condenser Tubes,Stainless Steel Tubular Condenser,Tubular Condenser For Fish Meal
RONGCHENG PINGFANG FISHERY MACHINERY CO., LTD. , https://www.pf-fishmealmachine.com