A news of "recharging one minute and cruising for 800 kilometers" took our eyes to the solid state battery. It seems that solid-state batteries have suddenly become a magic weapon for making electric vehicles leap. Although a closer look, it is not difficult to find that the news disclosed by Fisker Company still has a lot to discuss, but at least shows that solid-state batteries are becoming a new direction for battery development.
On the other hand, it has been said for many years that fuel cell vehicles have become the focus of attention in recent years as Japanese and Korean car companies have successively put into production. Solid-state batteries and fuel cells, who is the future direction of new energy vehicles? What difficulties will they face each other?
"Flexible, superior energy density solid-state battery", the patent of the US electric car manufacturer Fisker, claims to increase the electric vehicle's battery life to 804 kilometers, and the charging time is reduced to 1 minute. What this patent describes is actually a solid-state battery.
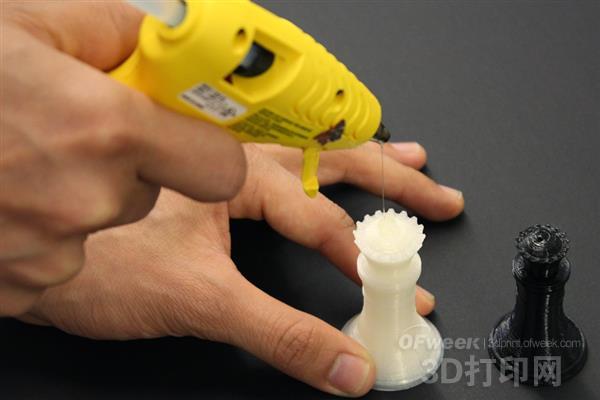
We may use simple physics knowledge to make simple calculations. According to the current 10kWh/100km energy consumption level of the electric vehicle, the 804 kilometers need 80.4kWh of energy. Then one minute is full of electricity, and the charging power will reach nearly 5000kW.
What is the concept of 5000kW? It is almost the power of a medium-sized power station. Therefore, the Fisker patent is only for laboratory data on single-cell solid-state batteries. In reality, taking into account the integration of the battery pack and the capacity of the grid, the so-called "charging for one minute, life of 800 kilometers" can only be a propaganda gimmick.
However, solid-state batteries are indeed an important direction for current vehicle power batteries to achieve energy density breakthroughs. Another development direction for fuel cell vehicles has also been advancing in recent years. Do not you see, when Tesla and Toyota mock each other's technical route, it means there must be a lot of articles to speak.
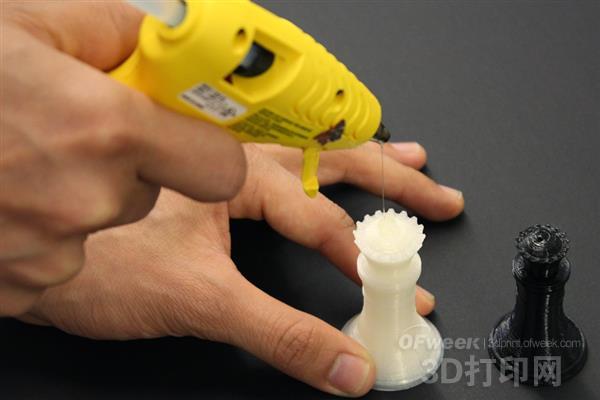
Solid-state battery: The breakthrough that enables pure electric vehicles to achieve large-scale commercialization
Every significant improvement in battery performance is essentially a major change in the battery material system. Because each type of battery material system has its upper limit of energy density.
From the first generation of nickel-metal hydride batteries and lithium manganese batteries, the second-generation lithium iron phosphate batteries to the third-generation ternary batteries that are widely used and are expected to continue to around 2020, energy density and cost are presented separately. The obvious trend of stepwise rise and fall. Therefore, what kind of battery system is used for the next-generation power battery is crucial for achieving the battery goal of around 2025.
The current lithium iron phosphate battery, the monomer energy density is approximately 120-140Wh/kg, the scale of the ternary battery monomer energy density can reach 130-220Wh/kg, the ternary battery in the laboratory can reach 300Wh/kg .
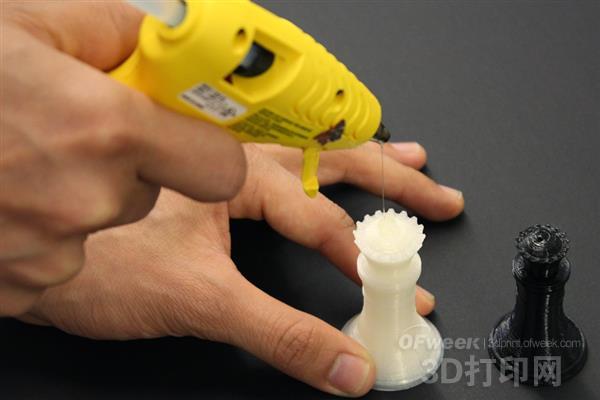
However, due to the influence of the existing system architecture and key cathode materials, the energy density of the lithium ion battery in the existing system is hardly to exceed 300 Wh/kg, and it is difficult to meet the demand of future power batteries. To reach the level of 400Wh/kg in 2025 and 500Wh/kg in 2030, the development and industrialization of emerging battery technologies is imminent, which means that the mileage of electric vehicles will double compared to the current one.
Currently, the main problem of commercial lithium-ion batteries is the use of liquid/colloidal electrolytes, which have limited electrochemical window and are difficult to be compatible with lithium metal negative electrodes and newly developed high-potential positive electrode materials, thereby causing a bottleneck in the increase of energy density. At the safety level, such an architecture can also cause problems such as short-circuit ignition, increased ion concentration, increased battery internal resistance, and continuous electrode material consumption.
The solid-state battery enters the field of view precisely because of its high ionic conductivity and mechanical strength, wide electrochemical stability window and operating temperature range, enabling high energy density, high power density, and high safety.
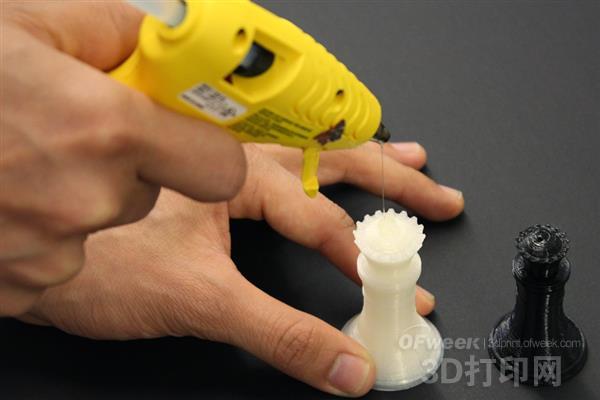
The solid electrolyte has a wider electrochemical window than the organic electrolyte, which is beneficial to further widen the voltage range of the battery, and can work in a large current condition because there is no concentration polarization, thereby increasing the battery energy density. At the same time, the solid electrolyte is non-flammable, non-corrosive, non-volatile, there is no leakage problem, no diaphragm is needed to separate the positive and negative electrodes, and the growth of lithium dendrite is prevented. The short circuit phenomenon of the battery is fundamentally avoided, and more negative electrode materials can be applied. .
In addition, when integrated into an electric vehicle, the solid-state battery also has features such as compact structure, adjustable scale, and large design flexibility, which facilitates integration of the entire vehicle.
It seems that the solid-state battery is not perfect? In fact, far from this. Current potential solid electrolyte materials can be classified into polymers, sulfides, and oxides. However, different materials and different combinations have very different chemical properties. Some have high charging speed, some have high energy density, and they have their own advantages. Each is short and it is difficult to achieve a material to solve all problems.
At the same time, the fact that the chemical properties are not stable and the preparation process is imperfect also has a long way to go for solid-state batteries.
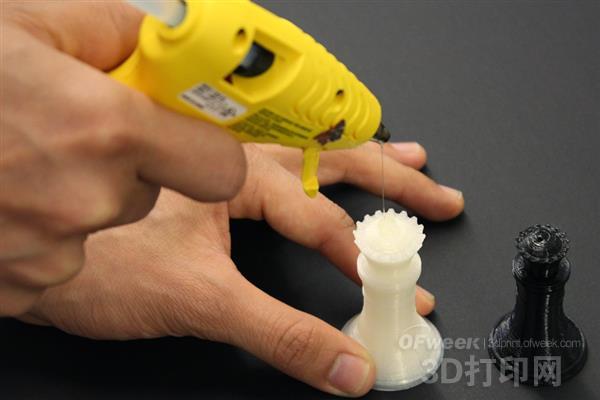
The realization of solid-state battery industrialization fundamentally depends on the breakthrough of the material process level. At present, the patent on solid-state batteries is far more comprehensive than other types of batteries. The industrialization of all-solid-state batteries with high energy density is expected to take 5-10 years. Some advanced companies will produce solid-state batteries in small quantities in 2020, and the real large-scale mass production is expected to be around 2025.
Fuel Cell: How to Realize a Profitable Business Model Is the Key to Popularization
In theory, hydrogen has a much higher energy density than electricity and oil. Of course, this means using hydrogen to generate electricity instead of directly burning hydrogen. In addition, it takes only a few minutes for a single hydrogenation and the driving range is 500-700 km. Only water is discharged during use, and there is no other exhaust gas. It is completely zero emission.
However, it looks like a very good fuel cell car to be truly commercialized on a large scale. There are three key issues that need to be addressed: the life of the fuel cell, the cost of the fuel cell, and the cost of hydrogen. To sum up, it is necessary to have a business model that can make every link in the industry chain profitable.
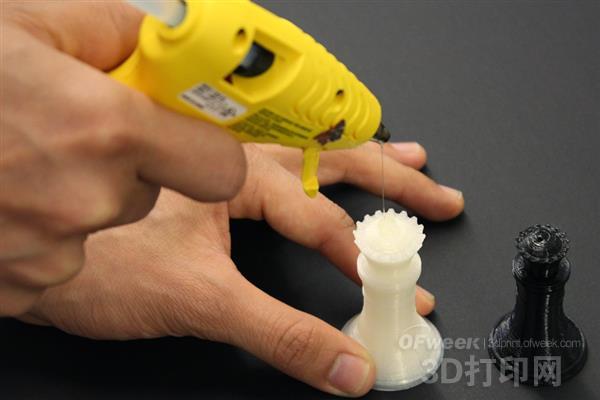
At the moment, if it does not rely on government subsidies, fuel cell vehicles are still in a state of “high priceâ€. The official guidance price of Datong FCV80, which was just listed at the Guangzhou Auto Show, reached 1.3 million yuan. After deducting the national 500,000 subsidy and local 500,000 subsidy, it still needs to spend 300,000 to buy this light passenger. This is obviously not feasible for fuel cell vehicles. Continuous development.
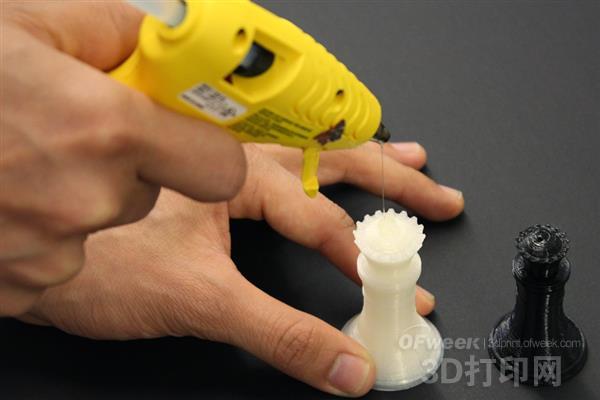
In addition to the general R&D investment, the amount of precious platinum in the catalyst is an important factor. Even with the current technological progress, the amount of platinum still reaches the level of 0.3-0.5 g/kW. So a 100kW fuel cell system will need about 30-50g of platinum, you can refer to the price of platinum jewelry in the next market, you can probably have a concept of this cost.
On the other hand, in the fuel cell system, a number of key components such as bipolar plates, air compressors, and DC boosting components have fewer R&D and production enterprises in China, and they have to rely on imports to a large extent, and are also domestic fuel cell vehicles. The reason for the high cost.
This is the cost of the car. The cost of hydrogen fuel is also a big problem. Hydrogen production methods mainly include hydrogen production from electrolyzed water and hydrogen from industrial by-products. The cost of the former can be more than 3 times that of the latter. However, because the fuel cell has a very high requirement for hydrogen purity (99.9%), electrolytic hydrogen is the main component during the small-scale demonstration operation.
During the Shanghai World Expo, the cost of hydrogenation of fuel cell vehicles is 70 yuan/kg, and the fuel cost per unit of mileage is even higher than traditional fuel vehicles.
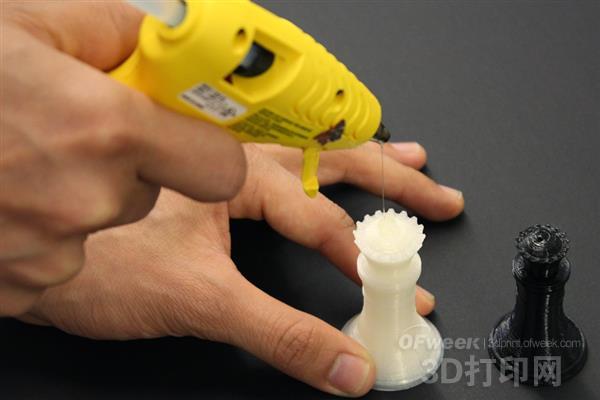
If renewable hydrogen such as by-produced hydrogen can be used, the price of hydrogen per kilogram will be around 20-30 yuan. For a car, it can run more than 100 kilometers per kilogram of hydrogen. For a car with the same level, it needs to run 100 kilometers. It costs about 8 liters of oil and it costs about 50-60 yuan according to the current oil price.
At this time, the use cost of fuel cell vehicles is only about half that of traditional fuel vehicles. Of course, the separation, purification, and distribution mechanisms of industrial by-product hydrogen must all be studied in depth and constantly improved.
In addition, the storage of hydrogen is also a key factor in the popularization of fuel cell vehicles. In order to obtain higher energy density, hydrogen is often cooled to below -253°C to become liquid storage. This not only requires high heat insulation performance of hydrogen storage containers, but also consumes more energy for liquefied hydrogen gas. One-third of hydrogen energy, which will greatly reduce the overall utilization of hydrogen energy on board.
In the hydrogen filling process, additional temperature-reducing measures must be taken to control the temperature rise of the gas cylinder, which is generally as low as -40°C. It can be imagined that this filling process requires much extra energy to achieve temperature control.
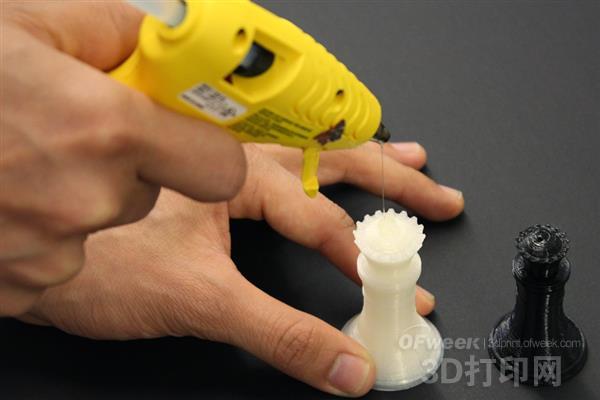
No matter which hydrogen production method, which storage method, or which transportation method, the hydrogen energy ecosystem needs to be re-established, involving a large amount of infrastructure investment and construction.
At present, there are only six hydrogen refueling stations put into operation in China. According to the national “Thirteenth Five-Year Planâ€, China will build 100 hydrogen refueling stations by 2020, but this is only the current level in Germany and Japan. Moreover, the construction cost of the hydrogen refueling station exceeds 10 million yuan, nearly 10 times that of the charging station, and the complexity of the intermediate links makes the construction of the hydrogen refueling station far more difficult than the charging station.
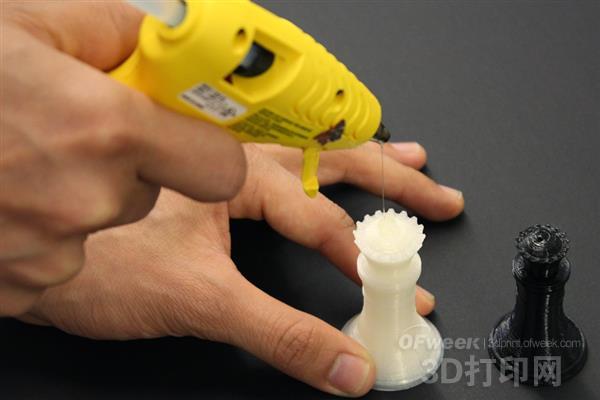
• Solid-state or fuel cells: Who can take the lead in resolving battery material systems and hydrogen energy ecology?
Who can represent the future of new energy vehicles? At least for now, there is no clear answer. On the one hand, the battery material system urgently needs to be upgraded in exchange for higher energy density; on the other side, the hydrogen energy ecosystem urgently needs to be established so that the fuel cell vehicle can go on the right track of the business model.
Obviously, the two issues that limit their respective developments will not be solved in a short time. This is why both parties have powerful members who are sticking to their own technology.
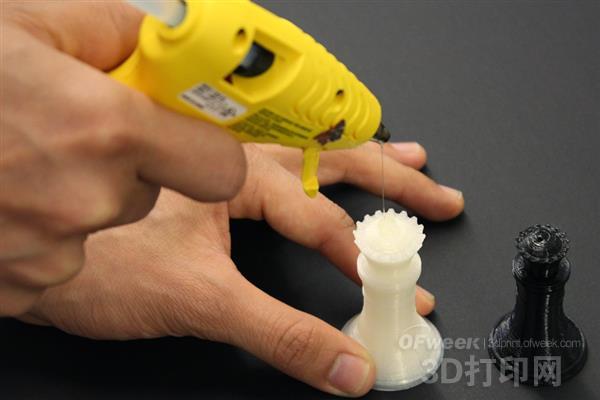
In the short term, pure electric vehicles will certainly precede the industrialization and popularization of fuel cells. Judging from the completion of the power system, pure electric vehicles can already be commercialized, and fuel cell vehicles will take time. After all, when Toyota Mirai was first put into production, the production capacity of three cars a day was hardly to be regarded as a true volume production. Even if Toyota plans to produce 30,000 cars a year by 2020, this year.
From the point of view of infrastructure construction, the construction of charging infrastructure in China, especially in the first- and second-tier cities, has begun to take shape, and most of the electric car users are no longer worried about not charging. Looking at the construction of hydrogen refueling stations, the technical and cost constraints are still huge challenges.
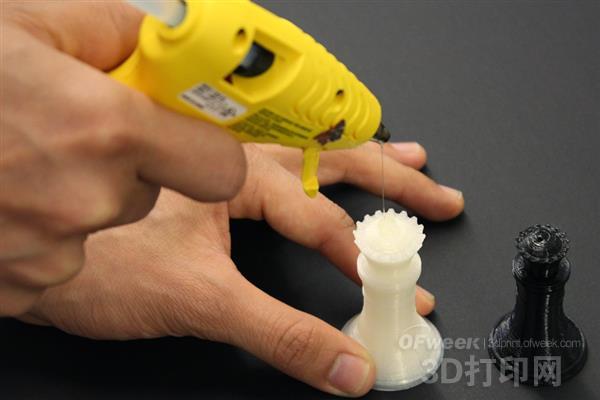
However, it is undeniable that the huge potential of fuel cell vehicles has not yet been developed. The current problems in various industrial chains cannot obliterate the advantages of the hydrogen energy ecosystem. This is why the industry generally regards fuel cell vehicles as the "communism" of automobiles. .
Only from the current point of view, whether it is technology maturity, consumer acceptance, promotion of feasibility or policy-oriented, creating a higher driving range of pure electric vehicles will become the common choice of car companies in the next 5-10 years.
brass fittings according to EN1254,the material is DZR602 and 754S,brass fittings,brass plumbing fittings,brass pipe fittings,connex brass fittings,yorkshire brass fittings,pegler brass fittings
brass fittings,brass plumbing fittings,brass pipe fittings,connex brass fittings,yorkshire brass fittings,pegler brass fittings
Taizhou Runde Company , https://www.zjbronzefittings.com