Application
A tree chipper or woodchipper is a machine used for reducing wood (generally tree limbs or trunks) into smaller woodchips. They are often portable, being mounted on wheels on frames suitable for towing behind a truck or van. Power is generally provided by an internal combustion engine from 3 horsepower (2.2 kW) to 1,000 horsepower (750 kW). There are also high power chipper models mounted on trucks and powered by a separate engine. These models usually also have a hydraulic crane.
Tree chippers are typically made of a hopper with a collar, the chipper mechanism itself, and an optional collection bin for the chips. A tree limb is inserted into the hopper (the collar serving as a partial safety mechanism to keep human body parts away from the chipping blades) and started into the chipping mechanism. The chips exit through a chute and can be directed into a truck-mounted container or onto the ground. Typical output is chips on the order of 1 inch (2.5 cm) to 2 inches (5.1 cm) across in size. The resulting wood chips have various uses such as being spread as a ground cover or being fed into a digester during papermaking.Most woodchippers rely on energy stored in a heavy flywheel to do their work (although some use drums).Â
Raw materialÂ
Pine wood, weed tree wood, poplar wood, fir wood, slab, veneer, bamboo, corm stalk, cotton, reeds and other non-wood fiber rod materials.
Â
Product Advantage
1.Advanced structure, high quality cutting chippers, wide scope of application, simple operation, easy maintenance;
2.Wear-resistant sharp alloy tool, reliable advanced and to enhance its service life;
3.Wearing parts low-consumption, low running cost.
Specification
Model | Power(KW) | Capacity(t/h) |
B215 | 45+4+3+1.5 | 2-4 |
B216 | 55+4+3+1.5+1.5 | 4-6 |
B218 | 110+5.5+4+1.5+1.5 | 8-12 |
B2113 | 220+7.5x2+1.5 | 15-20 |
Customer Visit
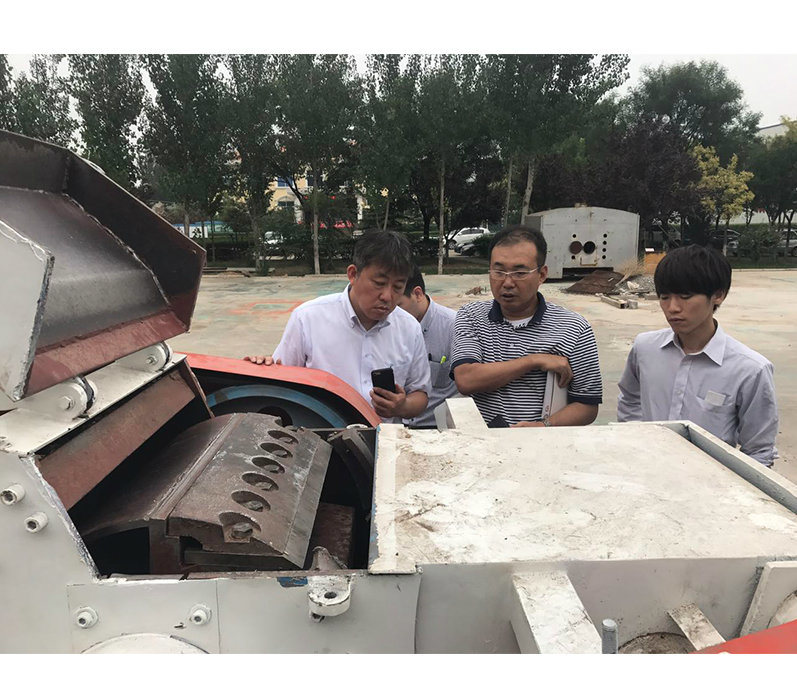
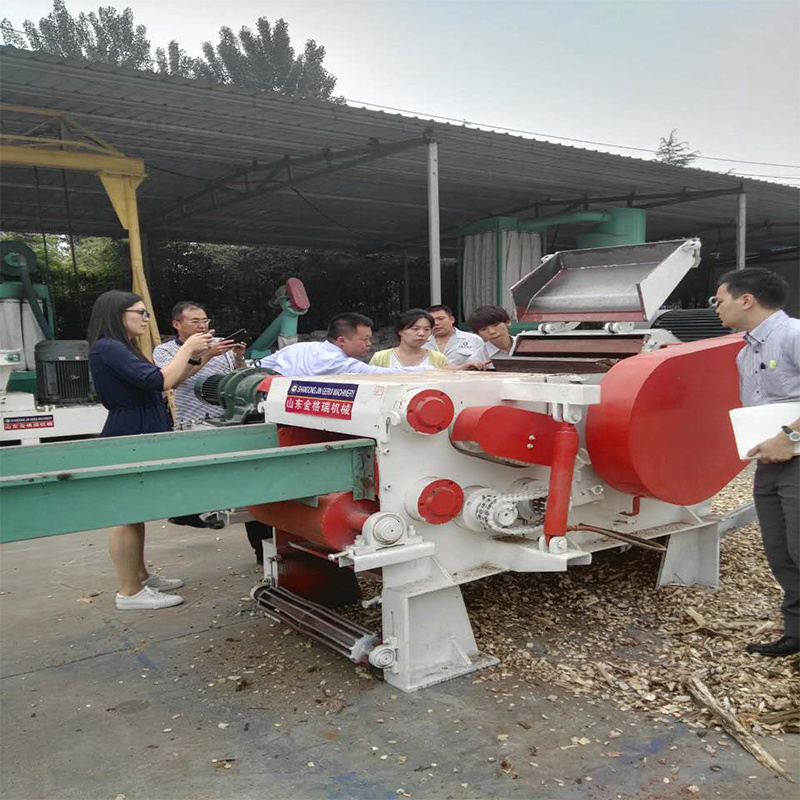
After-sales team
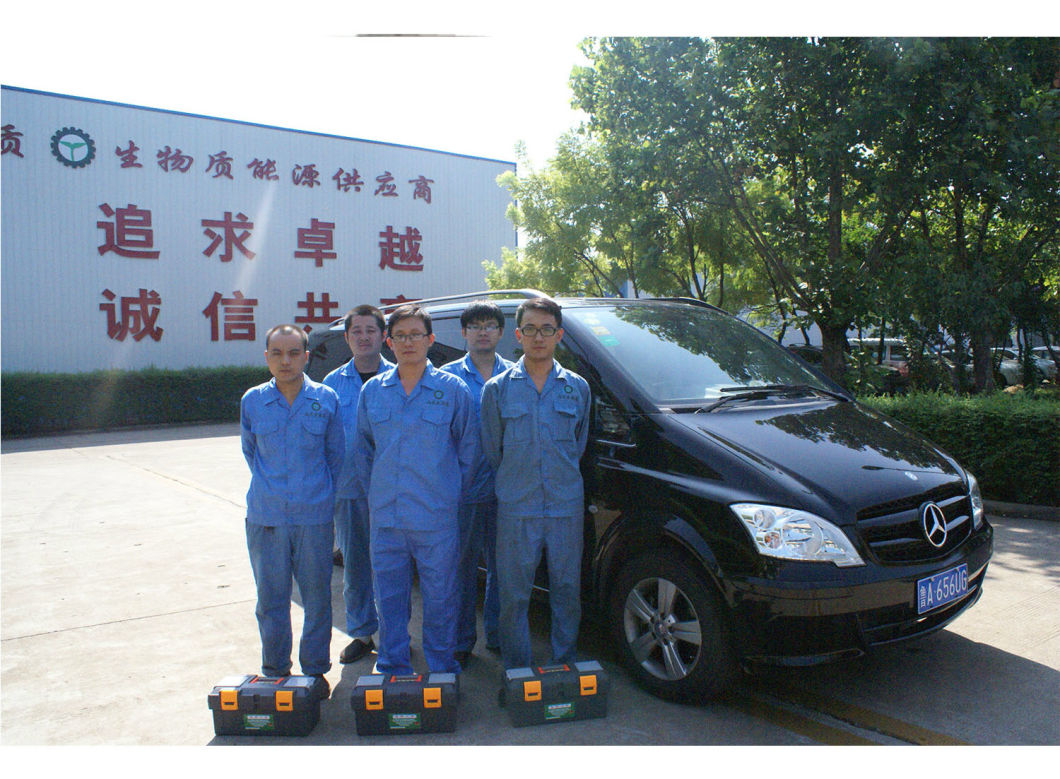
Â
Application
A tree chipper or woodchipper is a machine used for reducing wood (generally tree limbs or trunks) into smaller woodchips. They are often portable, being mounted on wheels on frames suitable for towing behind a truck or van. Power is generally provided by an internal combustion engine from 3 horsepower (2.2 kW) to 1,000 horsepower (750 kW). There are also high power chipper models mounted on trucks and powered by a separate engine. These models usually also have a hydraulic crane.
Tree chippers are typically made of a hopper with a collar, the chipper mechanism itself, and an optional collection bin for the chips. A tree limb is inserted into the hopper (the collar serving as a partial safety mechanism to keep human body parts away from the chipping blades) and started into the chipping mechanism. The chips exit through a chute and can be directed into a truck-mounted container or onto the ground. Typical output is chips on the order of 1 inch (2.5 cm) to 2 inches (5.1 cm) across in size. The resulting wood chips have various uses such as being spread as a ground cover or being fed into a digester during papermaking.Most woodchippers rely on energy stored in a heavy flywheel to do their work (although some use drums).Â
Raw materialÂ
Pine wood, weed tree wood, poplar wood, fir wood, slab, veneer, bamboo, corm stalk, cotton, reeds and other non-wood fiber rod materials.
Â
Product Advantage
1.Advanced structure, high quality cutting chippers, wide scope of application, simple operation, easy maintenance;
2.Wear-resistant sharp alloy tool, reliable advanced and to enhance its service life;
3.Wearing parts low-consumption, low running cost.
Specification
Model | Power(KW) | Capacity(t/h) |
B215 | 45+4+3+1.5 | 2-4 |
B216 | 55+4+3+1.5+1.5 | 4-6 |
B218 | 110+5.5+4+1.5+1.5 | 8-12 |
B2113 | 220+7.5x2+1.5 | 15-20 |
Customer Visit
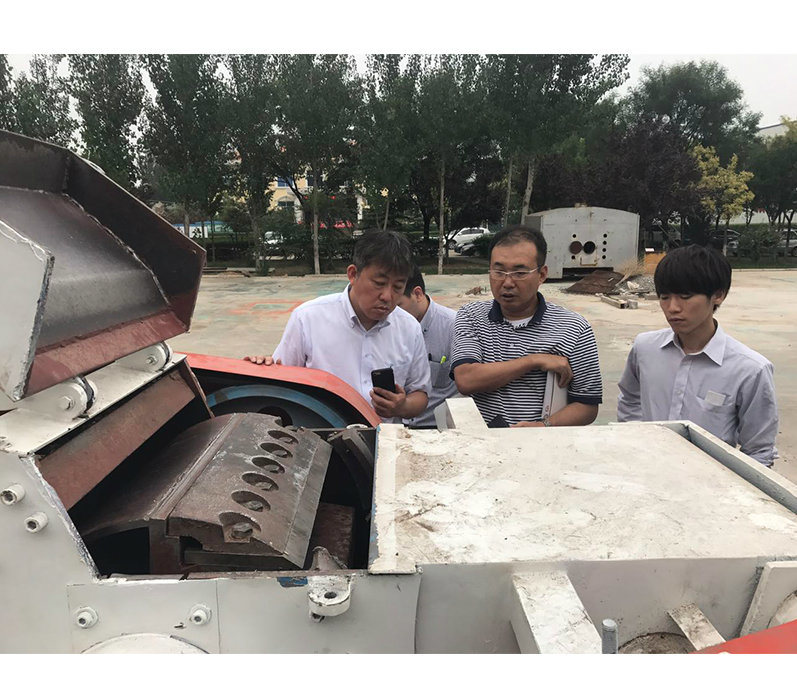
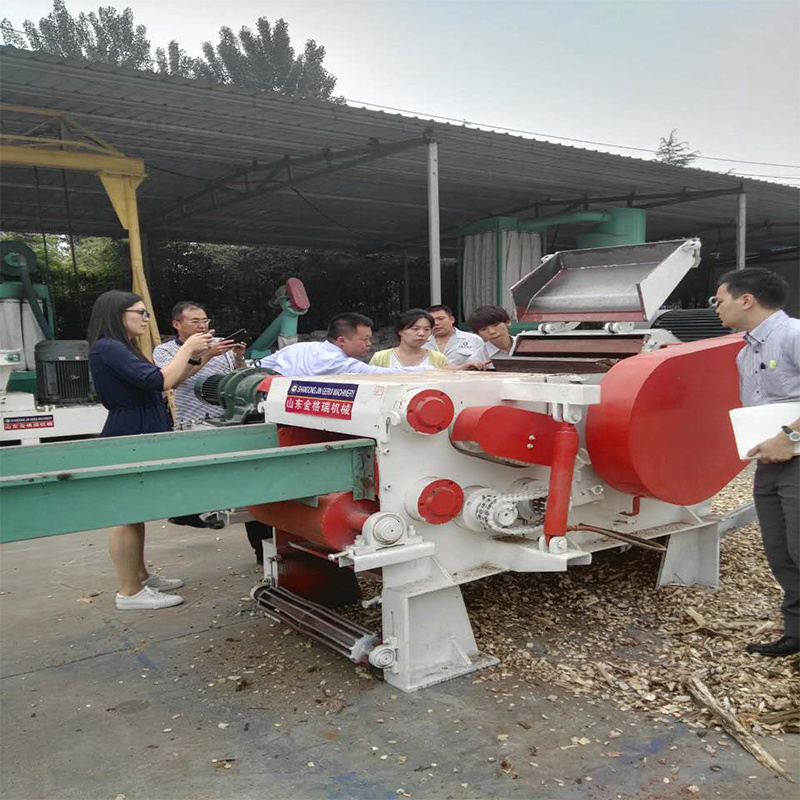
After-sales team
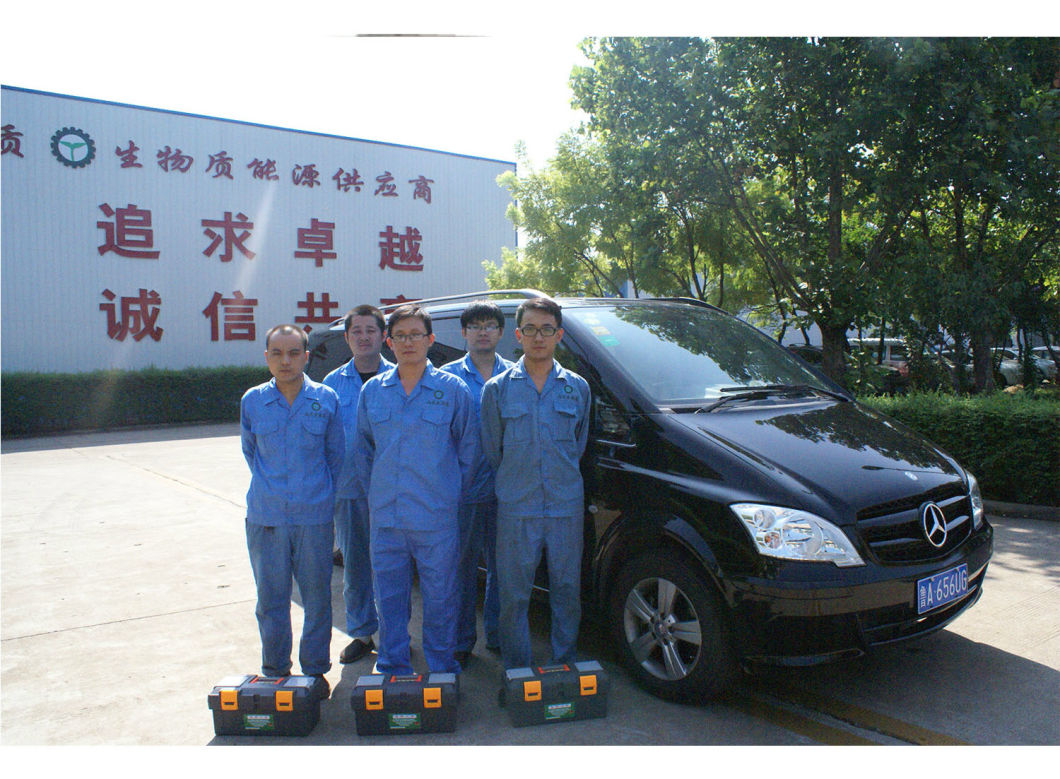
Â
Plastic Injection Insert Molding
1. The combination of the easiness of molding and bending of resin and the rigidity, strength and heat resistance of metal can make complex and sophisticated metal-plastic integrated products sturdily.
2. In particular, the combination of the insulation of resin and the electrical properties of metal can meet the basic functions of electrical products.
3. The pre-forming combination of multiple inserts makes the post-engineering of product unit combination more reasonable.
4. Insert products are not limited to metal, but also cloth, paper, wire, plastic, glass, wood, wire ring, electrical parts and so on.
5. For rigid parts and flexible parts on rubber sealing pad, the complex operation of arranging sealing ring can be eliminated after the integrated products are made by injection molding on the matrix, which makes the automatic combination of the following process easier.
6. Because it is the fusion of molten material and metal insert, compared with the pressing molding method, the metal insert gap can be designed to be narrower, and the reliability of composite product molding is higher.
7. Suitable resin and molding conditions may be used for sealing and fixation of susceptible products such as glass, coils, electrical parts, etc.
8. Inserts can also be completely sealed into the resin by selecting the appropriate mold construction.
9. After the insert is molded, it can also be made into a product with hollow grooves along with the core hole.
10. The combination of vertical injection molding machine and manipulator, the whole row device of insert products, etc., the insert forming engineering can be mostly automated production.
Plastic Injection Insert Molding,Washing Machine Plastic Injection Moulds,Plastic Injection Molding,Plastic Injection Molding Machine
Suzhou Dongye Precision Molding Co.,Ltd. , https://www.sjinjectionmolding.com