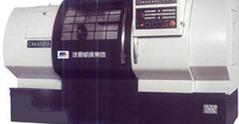
The economic growth of the industry is rapid and the growth structure is irrational. The economic growth of China's machine tool industry is rapid. In 2011, China produced a total of 860,000 gold-cutting machine tools and 238,500 molding machine tools, achieving a total industrial output value of 660.65 billion yuan. In recent years, the numerical control rate of China's production machine tools has increased, but compared with the United States, Japan and other countries, the numerical control rate is at a relatively low level. Among them, the numerical control rate of gold-cutting machine tools is about 30%, and the numerical control rate of forming machine tools. Less than 7%. In 2011, China produced 860,000 gold-cutting machine tools and 257,000 CNC machine tools. The output of CNC machine tools accounted for only 29.9% of the production of gold-cutting machine tools; the production of forming machines was 238,500, and the number of CNC machine tools was 15,000, and the number of CNC machine tools was produced. Only 6.29% of the output of forming machines.
The transformation will drive the RMB 350 billion yuan in the demanding market for numerical control transformation projects to generate industrial added value of several hundred billion yuan. There are more than 4 million ordinary machine tools in China, of which 1/4 of them are over 30 years old. These machine tools (more than 1 million units) have no transformation value and need to be eliminated; the remaining 3/4 (more than 300 Million units can be digitally modified. According to the previous general machine tool transformation experience of CNC, the average cost of transformation of small and medium-sized machine tools is between 30,000 yuan and 100,000 yuan, and the average transformation cost is about 60,000 yuan per Taiwan. (Note: Due to the maturity of CNC system technology and the increase in the number of production, the cost After declining and increasing safety requirements, the cost of reconstruction should not increase.) If more than 4 million ordinary machine tools are reformed and renewed, about 200 billion yuan worth of renovation needs and about 150 billion yuan will be needed for renovation (updating about 150,000 yuan per unit), which will play a role in maintaining economic growth. .
CNC transformation reduces costs and reduces resource waste. Compared with the purchase of new machine tools, ordinary machine tool CNC transformation can generally save 60% to 80% of the cost, especially for large and special machine tools. General large-scale machine tool transformation, only one-third of the cost of new machine purchases, such as the update of all the more than 400 million ordinary machine tools (updated costs about 150,000 yuan / Taiwan), about 600 billion yuan in costs, and numerical control The reconstruction has increased by about RMB 250 billion. At the same time of cost saving, the numerical control transformation can also save about 5 million tons of steel consumption and corresponding energy consumption and pollution emissions caused by all the updates.
CNC transformation to improve the efficiency of machine tools and reduce production costs. According to previous transformation experience, after the general machine tool is transformed into CNC, the efficiency of the machine tool can mostly be increased by 30% to 50%, and some even increase by more than 1 time. At the same time, the machining accuracy of the machine tool has been greatly improved, and the scrap rate caused by human error has been significantly reduced. At the same time, the labor intensity of the workers has been reduced, labor force has been saved (one person can look after multiple machine tools), tooling is reduced, and new ones are shortened. Product trial cycle and production cycle bring huge economic benefits to the company.
CNC transformation to improve the safety level of machine tools and reduce accident losses. After the ordinary machine tool completes the transformation of the numerical control, it can greatly improve the machining efficiency and automation and intelligence of the machine tool. The original one machine tool needed a person to control. After the transformation, a worker could control 2 to 3 machine tools at the same time, reducing the configuration of the operator; through the installation of protective isolation doors and safety interlock devices and other safety protection devices, the machine tool movement, The operating part and the operator can achieve safe and effective isolation, reducing the possibility of the operator touching the dangerous part; the operating system and the operation interface are more and more in line with ergonomic requirements, and the requirements for the operator's own ability are gradually reduced, which can effectively reduce The operator's error rate reduces accidents caused by mistakes. After the transformation of the machine tool by CNC, the safety performance has been significantly improved, and the accident rate has been significantly reduced, which will bring huge safety benefits. In the event of personal injury in the production process of the company, it will bring many losses, including paying the medical expenses for the injured, providing financial compensation to the injured, the loss of work stoppage caused by the employee's work stoppage, and the company's stopping the production. The loss of production suspension, the company was punished by the regulatory authorities.
GRP FRP Pultrusion Profile,Fiberglass Threaded Bolts,Fiber Bolts Nuts,GRP Frp Bolts
Hebei aoliande Chemical Equipment Co., Ltd , https://www.aoliandepipes.com