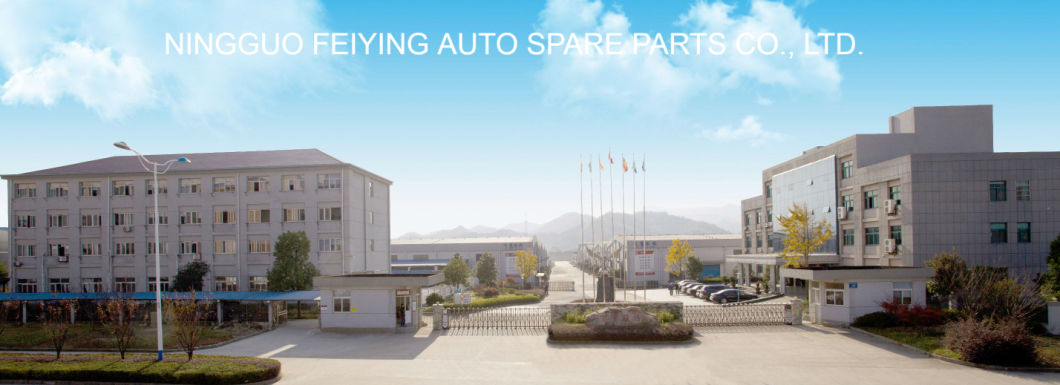
FAQ
1. Question: Are you a factory?
Yes. Our factory established in 1995, and we have been in auto parts business for 23 years. We have 80,000 square meters workshop and more than 260 employees.
2.Question: How is your facility?
We have 10 "800tons" hydraulic machines, 20 "500tons" and more than 30 small tons machines. We also have one brake lining automatic product line for international business only.
3.Question: what's your annual output?
We have 3 mature product lines. One is for brake lining, one is for clutch, and one is for brake shoe. Brake lining annual output is 8 million pieces, clutch is 300,000 sets, and brake shoe is 600,000 pieces.
4.Question: Why choose us?
First, we have more than 100 models for brake lining, so we are able to produce most of the products in the market. In addition, our advanced technology supports our products' quality. We have many different formulas targeting different markets and applications. We also pay attention to provide good service. We have a very professional team, and most agents have more than 10years experiences dealing with international business.
5.Question: what's your delivery time?
Normally, it's about 25-45days.
6.Question: how to ensure your product quality?
Material and test: Our technology department tests the material first before they put in raw material storage, we only pick the good material and use in workshop. We also use "chase machine" to test our products before deliver to picking line. Certifications: we have EMARK, TS/ISO16949, LINK and SABS.
-- Product Specifications
1.Excellent performance
2.Long durable life
3. Noiseless
4. Environment friendly, high temperature tolerance
                                 Brake Lining 19037  Non-asbestos | |
Product | Brake lining |
WVA Number | 19037 |
Material | Non-asbestos |
Size![]() Â |
Length outside:Â 206 Â Length inside:Â Â Â Â Â Â Â Â Width:177.8Â Â Â Thickness: 18.2/14.2 Â Â R:203Â Â Â Â Â Â Â Rivets:12 |
Application | DAF, SAE, SAD, Trailor, Castera, Crane,Kaiser,Steyr |
Life time | 60,000-120,000km in normal condition |
MOQ | 100sets |
Delivery time | 30-45days |
Port | WuHu |
Certification | EMARK, SABS, LINKÂ |
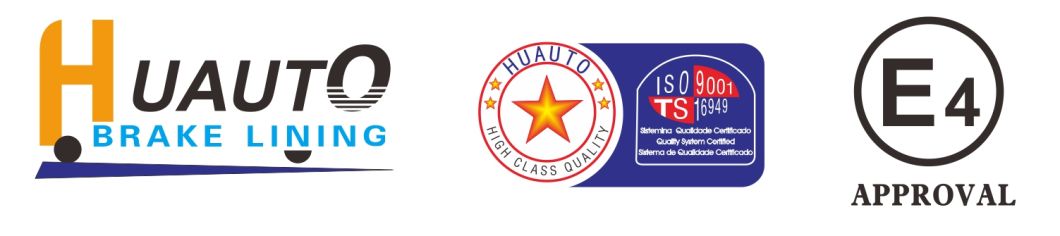
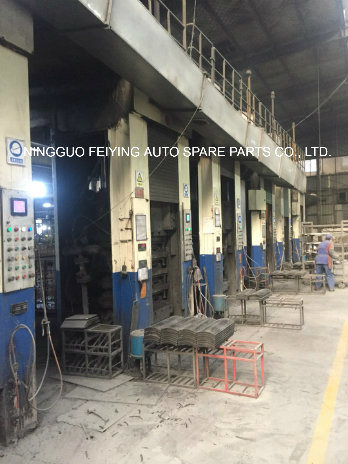
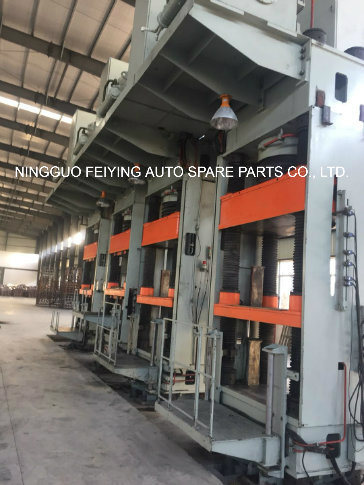
Heating insulation for a Brazed Plate Heat Exchanger is important to minimize heat loss and improve the overall efficiency of the system. Some common insulation materials used for this purpose include:
1. Mineral Wool: Mineral wool is a popular choice for insulation due to its excellent thermal properties and fire resistance. It is available in various forms, such as blankets or boards, and can be easily cut and shaped to fit the heat exchanger.
2. Foam Insulation: Foam insulation, such as polyurethane or polystyrene, is lightweight and offers good thermal insulation. It is often used in applications where space is limited or weight reduction is desired.
3. Fiberglass: Fiberglass insulation is widely used in industrial applications due to its low cost and good thermal insulation properties. It is available in various forms, such as batts or loose fill, and can be easily installed around the heat exchanger.
4. Ceramic Fiber: Ceramic fiber insulation is known for its high-temperature resistance and low thermal conductivity. It is commonly used in applications where the heat exchanger operates at high temperatures.
When selecting insulation for a brazed plate heat exchanger, it is important to consider factors such as the operating temperature, space limitations, and fire safety requirements. Additionally, proper installation and sealing of the insulation are crucial to ensure maximum effectiveness.
Titanium Pool Heat Exchanger Epp Insulation, heat exchanger heating insulation, brazed heat exchanger heating insulation
Jiangsu Baode Heat-Exchanger Equipment Co.,LTD , https://www.baodeexchanger.com