Introduction: Robots not only use the "eyes" for high-definition video capture, they also have "tactile sensation." Thermal imaging on the robot's motion platform uses infrared thermal imaging to measure the temperature of the cable connector, the temperature of the cable grounding box, and the fixed temperature of the cable surface; at the same time, the robot The "brain" has never stopped, and the handling and analysis of various parameters and even the analysis of gases in the environment are all in progress. And transmit these real-time data to the back-end center platform.
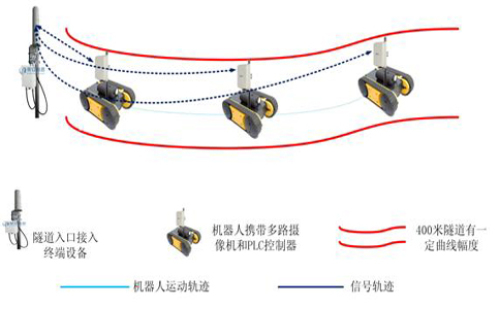
Power inspection robot application requirements
The traditional manual inspection method has the disadvantages of large labor intensity, low work efficiency, decentralized detection quality, and single means. The application of robots in the field of power inspection will become more and more popular. In fact, various meter values, switch positions, and sensor signals in the power distribution room are confusing, the weather in the substations is hot and cold, and the humidity in the cable tunnels is hot and humid, toxic gases, and electromagnetic radiation. These can be handed over to robots. .
The main function of electric robot
Robots not only use the "eyes" for high-definition video capture, they also have "tactile sensation," and the robot's motion platform uses infrared thermal imaging to measure the temperature of the cable connector, the temperature of the cable grounding box, and the fixed temperature of the cable surface; at the same time, the robot " The brain has never stopped. The processing and analysis of various parameters and even the analysis of gases in the environment are all in progress. And transmit these real-time data to the back-end center platform.
Project Introduction
In this project, the robot is mainly used in a tunnel with a depth of nearly 400 meters. The tunnel has a certain degree of curvature. The power patrolman puts the robot into the tunnel at the entrance of the tunnel, and uses the multiple surveillance cameras and sensors installed on the robot to transmit the various data and video detected by the robot in the tunnel to the patroller's mobile terminal equipment at the tunnel entrance. At the same time, the inspector can also control the robot. The customer was tested in a large number of various wireless devices in the early stage. Since the robot passes more than 10 isolated spaces in the tunnel, each compartment has only an open channel with a height of less than 80 cm and a width of no more than 40. Therefore, with the deepening of the tunnel, the transmission of wireless signals is more attenuated. If traditional networking and wireless bridging networking are used, data transmission in this case cannot be satisfied. After a number of different wireless deployments at multiple points in the tunnel, they eventually ended in failure.
The customer and the company's technical and technical personnel have conducted in-depth discussions, analysis of site conditions, robot working conditions, transmission requirements and other comprehensive analysis. We have designed a more feasible solution for our customers. According to the information provided by the customer, the robot is inspected in the tunnel. From the tunnel entrance to the tunnel terminal, the detection robot does not need to turn heads and straight forward, and the tunnel itself is not too far away, and the curve is not large. Through these points, we use the LA-5839A directional bridging transmission for the robot body to concentrate the signal farther. The LA-5839A has high-sensitivity reception and can obtain higher receiving sensitivity and link signal in the tunnel. It can fully meet the requirements of detecting robot data transmission. From the entrance of the tunnel through the packet access, the overall delay is basically around 2 milliseconds, and it can be well mastered and controlled for robot activities. Completely meets the bid requirements of the user.
As shown below
"Robots are replacing manual inspections by themselves. Once there is any disturbance in the substation, it will be reflected by the station control system. At present, both the State Grid and China Southern Power Grid have proposed to actively promote the integration of control and operation modes, and will automate and artificial intelligence. High-tech and cutting-edge robots such as computers are used as an important force in promoting the 'Industry 4.0' process in the electric power industry. From electric power intelligence to industrial intelligence, the current artificial intelligence field is also included. In the future, while the existing business is developing steadily, Promote the industrial upgrading of industrial robot applications and actively expand the intelligent logistics industry chain. At the same time, we will also adopt a combination of production, study and research cooperation and resource integration to promote the strategic deployment of 'artificial intelligence + health'.
Packing box,Corrugated Box Black,Box Cardboard Corrugated
Yutian Jifu Paper Products Co., Ltd. , https://www.yutianjifu.com