Recently, Kobe Steel Co., Ltd. of Japan delivered the complete set of the world's largest super-large container ship crankshaft to Mitsui Shipbuilding. The crankshaft has a total length of 22 meters and weighs about 500 tons. It has been developed by Kobelco in 2014 to increase the design fatigue strength by 20%. Manufactured by the "Modular Forging Method". In addition, the type of ship that transmits engine torque to the intermediate shaft of the propeller also uses Kobelco's unique high-strength material technology.
In recent years, the shipbuilding industry has become increasingly large in order to achieve efficient sea transportation. From 2011 to 2016, although the number of ships in the container fleet increased by only 5.3%, the load capacity (according to the number of TEUs) increased by 40%, showing a trend of large-scale. Therefore, the demand for very large crankshafts for container ship engines is also increasing.
Last year, Kobelco delivered the same type of crankshaft used by two ships. The crankshaft was used for the third ship. It is understood that the same model of the ship is expected to build a total of more than a dozen, including the delivered crankshaft, Kobelco plans to complete delivery by 2018.
Kobelco's crankshaft (assembled and integrated) has a global market share of 40%, and the intermediate shaft and propulsion shaft have a market share of 80% in Japan. It is the world's top manufacturer of cast-forged steel for ships.
In October last year, Kobelco became the only company in the world to manufacture k-factor=1.05 class certification for large to small cranks. K-factor is a coefficient in the design fatigue strength calculation formula. Its usual value is generally 1.00, and if high-strength materials of Kobe Steel are used, the strength can be calculated according to the coefficient of 1.05, creating a margin for the design.
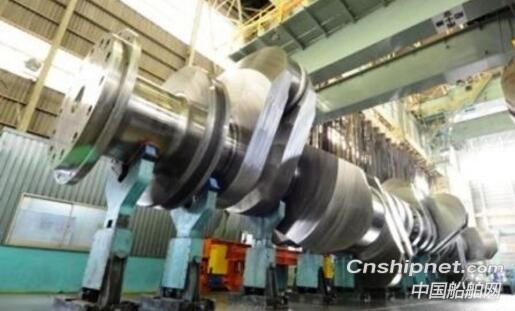
Last year, Kobelco delivered the same type of crankshaft used by two ships. The crankshaft was used for the third ship. It is understood that the same model of the ship is expected to build a total of more than a dozen, including the delivered crankshaft, Kobelco plans to complete delivery by 2018.
Kobelco's crankshaft (assembled and integrated) has a global market share of 40%, and the intermediate shaft and propulsion shaft have a market share of 80% in Japan. It is the world's top manufacturer of cast-forged steel for ships.
In October last year, Kobelco became the only company in the world to manufacture k-factor=1.05 class certification for large to small cranks. K-factor is a coefficient in the design fatigue strength calculation formula. Its usual value is generally 1.00, and if high-strength materials of Kobe Steel are used, the strength can be calculated according to the coefficient of 1.05, creating a margin for the design.
Duck Feather Camel Back Badminton
Cork Duck Shuttlecock,Cork Shuttlecock Badminton,Duck Camel Back Badminton,Cigu Duck Feather Camel Back Badminton
Shaoxing Love Feather Import And Export Co.,Ltd. , https://www.shengpaibadminton.com