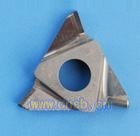
New Tool Material CNx
In recent years, there has been a new tool material carbon nitride. American physicists AMLin and ML Cohen used molecular engineering theory to design a novel superhard inorganic compound CNx. Based on the calculation of the bulk modulus, this compound can reach a hardness that is close to or even exceeds that of boron nitride and diamond.
Using the de-active magnetron sputtering process, physical and material scientists at home and abroad can deposit CNx superhard films on different substrate materials. This film has high hardness, high wear resistance, low friction and strong thermal conductivity, etc. Hanyang Technology does not react chemically with ferrous metals.
1.CNx film mechanical properties The domestic physicists deposited CNx thin films on high-speed steel cutters and carbide cutters. Their surface microhardness was measured to be 4000 to 7,200 HV. It can be seen that its hardness has reached the hardness of cubic boron nitride, but slightly lower than the hardness of synthetic diamond. Others have used the scratch method to measure the adhesion of the CNx film coating to verify that it meets the JB/T8365 standard.
2. Experiments on CNx surface coating tools (1) CNx surface coating HSS tool drilling experiments The author used a M2 (W6Mo5Cr4V2) high-speed steel twist drill with a diameter of φ10.5mm to coat the surface of CNx with a coating thickness of 3? 5μm. The same drill bit before and after the coating was drilled on a high-strength steel 38CrNi3MoVA (after tempering, hardness 36?40HRC) with a hole depth of 12mm.
Cutting amount: Feed rate f=0.13mm/r, speed n=600r/min, cutting speed v=19.8m/min; no cutting fluid added. Under such conditions, it takes about 9.6 s per hole to drill, and the tool wear value VB is measured on the flank at the maximum diameter of the drill. At the same time, in order to compare the different coatings, I also used the conventional PVD process TiN surface coated M2 high-speed steel twist drill, and the above twist drill together with the drilling experiment.
If 0.3mm flank wear is blunt, then CNx drill bits can drill 48 holes, which is about 8 times that of uncoated drills and 2 times that of TiN coated drills. It can be seen that the effect of CNx coating on the improvement of wear resistance is very significant. The number of drilled holes in the TiN coated drill bit is 24. The number of holes in the uncoated M2 drill bit is six.
(2) Turning experiment of CNx surface-coated hard alloy insert 1 The author used K30 cemented carbide insert as substrate to coat CNx film and turned T12A hardened tool steel (hardness 61HRC). It was compared with the uncoated K30 blade, and a cubic boron nitride (PCBN) turning tool was also included for comparison.
Cutting amount: cutting depth ap=0.5 mm, feed rate f=0.1 mm/r, cutting speed v=60 m/min.
Tool geometric parameters: rake angle γo=0°, relief angle αo=8°, lead angle κr=90°, edge angle λS=-4°, radius of nose radius rε=0.8mm.
When unhardened K30 hard alloy inserts were used to cut hardened tool steels, the flank wear loss VB was 0.3 mm at only 3 min. CNx coated inserts have a cutting time of 15 minutes when VB reaches 0.3mm.
The PCBN lathe cutting 20min, VB square 0.2mm. It is expected that the service life of PCBN turning tools can exceed 30 minutes.
2P20 cemented carbide inserts were used as the substrate, CNx film was coated, and 60Si2Mn high-strength steel was turned (quenched and tempered, hardness 40HRC). Compare with uncoated P20 blades. Also participating in the comparison is a TiC surface coated carbide insert made of CVD technology called YBo2.
Cutting amount: cutting depth ap=1mm, feed rate f=0.15mm/rwww.ZAOCHE168.COM, cutting speed v=150m/min.
Tool geometric parameters: rake angle γo=4°, relief angle αo=8°, leading angle κr=45°, cutting edge inclination λs=-4°, radius of nose radius rε=0.8mm.
The blunt standard is VB=0.3mm, the cutting time of uncoated P20 blades is only about 10min; the cutting time of YBo2 blades is about 30min, which is 3 times that of P20. After 30 min cutting of CNx coated blades, the VB is only 0.15 mm; when the VB reaches 0.3 mm, the cutting time can reach 40 min.
Analysis and Discussion From the above experimental study, it can be seen that the hardness of CNx-coated tools can reach the level of PCBN and close to that of diamond. The cutting effect is significant, and its service life is much higher than uncoated high-speed steel tools and carbides. Tool, also higher than TiN, TiC coated tool. And CNx and ferrous metals are inert and have no chemical effect. At the same time, moc.swenaii.WWW, C and N resources are abundant, there is no shortage of resources. From this analysis, CNx coated tools have great prospects for development and application prospects.
However, it is worthy of special attention to note that, given that the basic work of CNx-coated tools is still not enough, the following aspects must be taken seriously:
(1) Comprehensive testing of the mechanical and physical properties of CNx, such as tests for density, thermal conductivity, strength, elastic modulus, and impact value, should be implemented.
(2) High-speed steel drills have achieved significant cutting results with CNx coating. In addition, the drill bit can be used for coating without additional refinement. Other high-speed steel tools, such as turning tools, milling cutters, taps, gear hobs and pinion cutters, are waiting to apply CNx one by one to conduct experiments to fully examine the cutting results.
(3) In addition to turning tools, CNx should also be applied to other carbide tools (such as milling cutters, especially solid carbide drills, end mills, etc.) for cutting experiments.
(4) As a substrate, the binding force between various cemented carbides and CNx coatings is to be studied, so that the best cemented carbide base material is selected. At the same time, pre-coating of CNx coated carbide tools should also be studied.
(5) Nowadays, various new coating methods and types of coating materials have appeared one after another, such as TiAlN, TiCrN, Al2O3 and multi-layer coating, and they need to be compared with CNx-coated tools to further determine the use value of CNx coatings. .
(6) Explore the possibility of generating CNx thick films.
In short, after doing the basic work of the CNx-coated tool, it is popularized and applied. If you are eager for quick success, you can often only “want to be slowâ€.
Ningbo Metal Sharing Supply Chain Management Co., Ltd , https://www.metalsharing.com