Reasonable configuration.
0 Introduction Compressed air has good application performance, as an important power source, widely used by industrial enterprises to drive various pneumatic and pneumatic tools; control instruments and automation devices; scientific research; products and zero The airtightness test of the components; the bag air blowback of the dust removal system, etc., at this time, the supply pressure of the compressed air is generally within 0.8 MPa, and the flow rate belongs to the medium and small range, and some of the gas devices have high purification of the compressed air. Degree and dryness requirements, therefore, in determining the compressed air system equipment, we must fully consider the technical performance of various major equipment, while taking into account the system's safe production, environmental protection, energy conservation, etc., to achieve advanced technology and economic rationality When establishing the 443 quality compressed air system required for the dust removal system in the grain storage industry, based on the design principles of the compressed air station, the performance comparison and technical and economic analysis of the existing domestic air compressors and dryers are carried out. Finally, the reasonable configuration of the system equipment was selected. The implementation of this process has certain reference for the equipment selection of compressed air system in the future. 1 System Overview The compressed air system designed by us is used for the dust removal system in the grain storage operation industry, and is used for the bag filter of the pulse bag type dust collector. Blowing, the maximum gas consumption of the system Qmax=328m3/min, the highest working pressure P=0.8MPa, the compressed air is required to reach the oil-free and anhydrous 443 quality, continuous gas supply, centralized control in the central control room, 1m away from the equipment, the noise is less than 85dB. Working condition and design calculation, under the rated working pressure of 0. 8MPa, the rated displacement of 40m3/min can meet the system requirements, and then consider having a spare unit. The system can be equipped with three rated exhausts of 20m3. /min, the rated working pressure is 0.8MPa air compressor, in order to facilitate flexible allocation of gas supply, and reduce the investment cost of spare equipment, and then equipped with degreasing, water removal, drying and other equipment, to achieve system requirements, equipment configuration is easier to carry out, A lot of work still falls on the selection of equipment. With the development of economic technology, the situation that industrial enterprises mainly use piston air compressors has been broken, air compressors and compressed air nets. The competition in the chemical equipment market is fierce. For this reason, we conducted a market survey on the main equipment air compressors and dryers in the system, and made a comprehensive comparison of performance investment, operation, maintenance, etc., and finally selected the appropriate space for the system. Main equipment such as presses and dryers.
2 Main single-unit equipment performance comparison and economic and technical analysis 2.1 There are many types of air compressor air compressors. In terms of the wide range of current use, there are basically three main types: piston type, screw type, and centrifugal type. These three air compressors have their own advantages and disadvantages. Because our air compressors have a gas production capacity of 20m3 /min, which is a small and medium-sized air compressor, it is not suitable for the centrifugal air compressor to invest in the performance of the piston screw air compressor. The comprehensive comparison of operation, maintenance and other conditions is shown in Table 1. From the above comparison, we can see that the screw air compressor is our future development direction, especially for modern enterprises, using screw air compressor for unmanned operation and management. And control, easy to achieve mechatronics management. In foreign countries, the application of screw air compressors has been very extensive. In Japan, the market share of screw air compressors is about 70%. In the United States, the market share of screw air compressors is about 65%. In the European market, screws The occupancy rate of air compressors is about 60%. The market share in the domestic market is also increasing year by year. According to industry statistics, in 1987, 3~40m3/min air compressor, screw air compressor 1 (94 air compressor accounted for %) So far, screw air compressors have increased by a large proportion each year. Table 1 piston type screw air compressor performance, investment, operation, maintenance, etc. Comprehensive comparison project piston air compressor screw air compressor main equipment It is bulky and complex.
High speed, compact structure, small size, no unbalanced mass, no special foundation required.
One-time investment is low, there is a high investment, and there is no additional investment.
The gas produced by the gas quality is discontinuous, the gas pressure is pulsed; the exhaust gas temperature is high, the pipeline system is easy to deposit carbon, and the gas production quality is low.
Continuous gas production, stable gas pressure; low exhaust gas temperature, not easy to deposit carbon in the pipeline system, high gas production quality, gas production capacity below 60m3/min, high efficiency, low efficiency, low cost of wearing parts, and cumbersome maintenance and repair. The cost of use is high.
The rotor is operated in non-contact mode, no wear, less maintenance and repair work, low cost of use. It is required to set the cooling water circulation system without noise. The sound insulation cover is used. The noise is up to the national standard. The operation management must be carried out by others. Operation, interlock control can be implemented. 22 The dryer is equipped with a regenerative dryer with or without heat, micro heat and heat. The three commonly used dryers include a cold dryer and an adsorption regenerative dryer. According to the economic technical performance analysis of the type of dryer, see Table 2, the winter temperature in the northern region is low, so it is not suitable for the selection of the dryer. The economics, technical and performance analysis of the non-heating, micro-heat and heat-regenerating dryer are not hot. Regeneration dryer with thermal regenerative dryer micro-thermal regeneration dryer working principle pressure swing adsorption regeneration (PSA method) temperature-temperature adsorption regeneration (TSA method) pressure swing adsorption regeneration temperature adsorption adsorption drying degree (atmospheric dew point c) adsorption tower relative size minimum work Pressure / bar regeneration gas temperature / c cycle (full) cycle / h adsorbent type aluminum glue, molecular sieve heating equipment without large and medium regeneration gas consumption (7bai) 1 view ~ disc price than energy consumption / kW comprehensive review advantages of simple structure, One-time investment with low regeneration gas consumption is small and the work cycle is long.
It combines the advantages of both PSA and TSA and avoids its weakness. It belongs to the third-generation adsorption dryer. The comprehensive economy and technical indicators have good shortcomings. The regeneration gas consumption is large and the switching is frequent.
The structure is complicated, and the manufacturing and use cost is high.
Applications are small and medium. Medium and high pressure medium and large. Low pressure medium and large. Low and medium pressure! Taking the following process flow 3 detailed process flow chart shown in inki.net From the above analysis table, we can see that the micro-heat regeneration dryer is the first choice of three dryers, which combines the advantages of the first two dryers, avoiding Its shortcomings are a new generation of products with a wide range of applications. 3 System rational configuration 3.1 Selected equipment According to the operating conditions of the system and the comparison of the main equipment of the same level, we have selected the fixed low noise screw for the main equipment air compressor. Air compressor, three sets, each working flow Q=20m3/min, pressure P=0.8MPa; the main auxiliary equipment dryer uses micro-heat regeneration dryer, two sets, each working flow Q=40m3/min; For other auxiliary equipment, we have equipped the original US particle filter and high efficiency aggregate filter 3.2 Process flow Based on years of work experience and theoretical calculation of the system, we set the process layout of the compressed air system. Screw air compressor; 2. Gas storage tank; 3. Crude filter; 4. Liquid gas separator; 5. Micro heat regeneration dryer; 6. Crude filter; 7. Waste oil collector. 4 system configuration summary 4.1 three air compressor interlock control due to the start of the dust collector depends on the start of the belt conveyor on the grain storage and transportation line, the different transport lines, the open dust collector is also different, so the compressed air used to blow back the bag The amount is uncertain. Therefore, we have selected an interlock controller to interlock control of three air compressors. We always ensure that two air compressors are in working condition, and one is used as a backup, which is flexible and saves energy and cost. When one of the two air compressors in the work fails, the standby machine automatically cuts into the start of the 4.2 gas tank. We designed the front of the gas tank, in addition to ensuring that the system gas is stable, it can also be considered The outlet air temperature of compressed air separates the impurities such as water and oil in the compressed air with the decrease of the temperature of the compressed air, which is beneficial to prolong the life of the post-treatment equipment and improve the quality of the compressed air. 4.3 After-treatment system uses a liquid-gas supply The separator starts, the whole system is divided into two ways, one for each device, and one system is always in normal working state.
Metals, alloys and composite powders commonly used in thermal spray hardfacing technology and coating service. These unique powders are instantly heated by thermal spraying (welding) methods such as high temperature flame or explosive flame, and are sprayed and deposited on the cold or hot workpiece surface with high-speed heat flow in a molten or semi-melted state to form a surface Reinforcing layer, in order to improve the wear resistance, corrosion resistance, heat resistance, oxidation resistance or repair of external dimensions of the workpiece surface. XTC produces WC, CrC, Oxide Ceramic, Boride Powder, Metal Alloy Powder, Pure Metal and Spray Wire, etc. product. For HVOF/HVAF/plasma/Flame spray coating and applications. Meet the wear and corrosion resistance requirements of different surfaces.
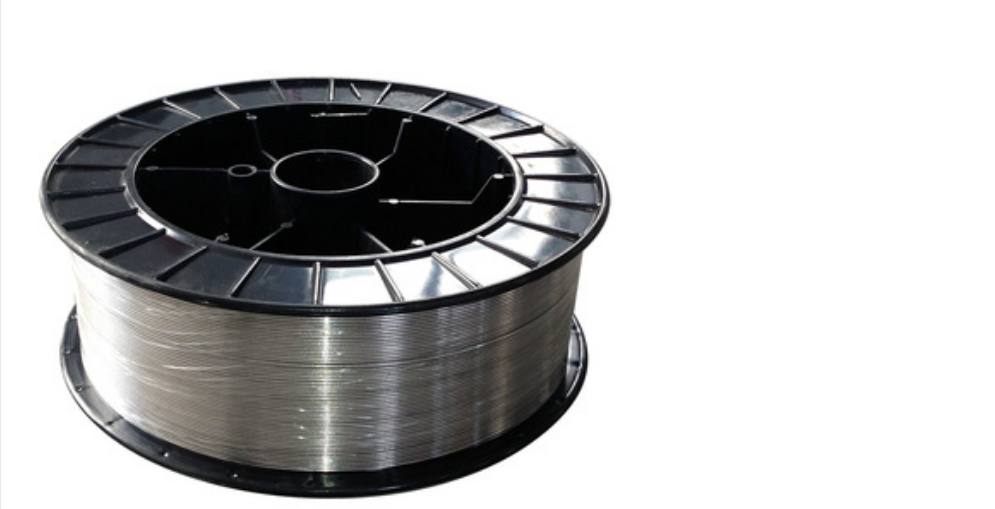
WC, CrC oxide ceramic powder and boride products are excellent in wear resistance and high temperature corrosion resistance. Taking WC products as an example, the hardness can reach HV1300-1500, and the temperature of CrC products can reach 800 degrees Celsius.
Metal alloy powder, Pure Metal and Spray Wire products have more applications in glass mold, steel and machinery industries. And XTC products are now become more and more popular in Metal spray coating and thermal spray coating industry.
Coating Service,Metal Spray Coating,Flame Spray Coating,Thermal Spray Coating
Luoyang Golden Egret Geotools Co., Ltd , https://www.xtchvof.com