1. Hydrolysis methods and technical conditions and indicators
Hydrolysis includes both dilute hydrolysis and neutralization hydrolysis. In the case of dewatered dilute good hydrolysis and it should not be used in hydrolysis, and the hydrolysis is only applicable to very complex anode sludge and concentrate infusion Jamesonite lead ore reducing solution.
The dilute hydrolysis is carried out at a normal temperature, and the hydrolyzate is controlled to contain Sb3+1 to 2g∕L, and the amount of water added is calculated by the formula (1). After dehydration, the mixture was stirred for 10 to 20 minutes; the chlorinated filter cake was washed with pure water for 8 times or more. The numerically controlled hydrolysis rate of the neutralization hydrolysis process is 45% to 50% when the lead anode mud is used. 85% is used for the Changpo brittle sulphur concentrate, and the ammonia or soda is used as the neutralizing agent, and is calculated according to formula (2). The amount of addition, the washing requirements are the same as the dilute hydrolysis process. If necessary, some compounding agents are added during the hydrolysis to improve product quality. The hydrolysis rate is very high (≥95%). The hydrolyzate contains ∕1g∕L.


Second, the hydrolysis process
When the reducing solution is added to the clarified water, SbCl3 begins to hydrolyze, producing some unstable intermediates:

The slurry is very viscous and requires agitation, followed by an obvious dehydration process:

Sb4O5Cl2 with good filtration performance is prepared. After dehydration for 10-20 min, the agitation was stopped, and then the supernatant was extracted, and then the chlorination of the bottom was filtered. For medium-sized and above factories, it is better to filter with a filter. The filter is equipped with a filter section and a washing section. It is washed with pure water to ensure clean chlorination, continuous filtration, and low labor intensity. Small-scale plants are filtered using a vacuum suction tank. After the hydrolyzate is filtered, the filter cake is washed with pure water for 8 times or more to ensure the cleaning of the impurity elements.
Metals, alloys and composite powders commonly used in thermal spray hardfacing technology and coating service. These unique powders are instantly heated by thermal spraying (welding) methods such as high temperature flame or explosive flame, and are sprayed and deposited on the cold or hot workpiece surface with high-speed heat flow in a molten or semi-melted state to form a surface Reinforcing layer, in order to improve the wear resistance, corrosion resistance, heat resistance, oxidation resistance or repair of external dimensions of the workpiece surface. XTC produces WC, CrC, Oxide Ceramic, Boride Powder, Metal Alloy Powder, Pure Metal and Spray Wire, etc. product. For HVOF/HVAF/plasma/Flame spray coating and applications. Meet the wear and corrosion resistance requirements of different surfaces.
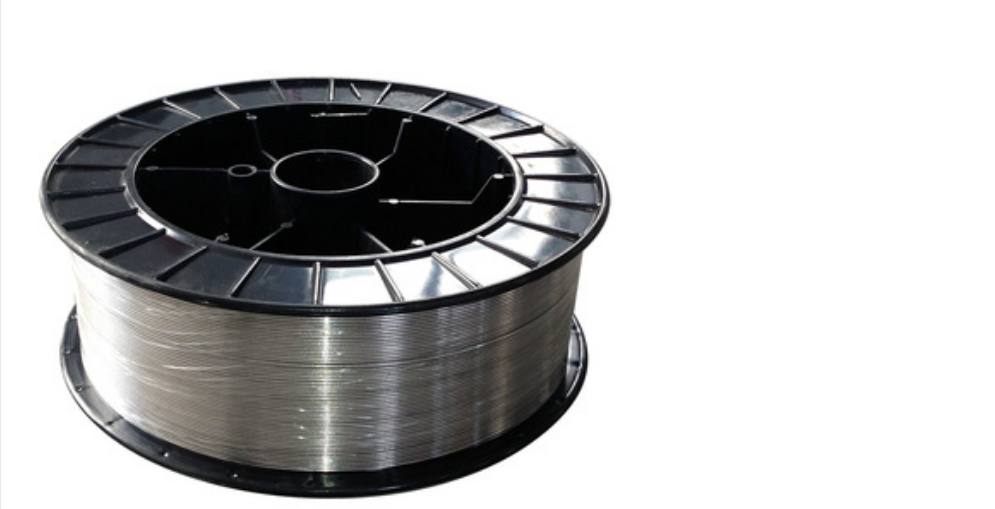
WC, CrC oxide ceramic powder and boride products are excellent in wear resistance and high temperature corrosion resistance. Taking WC products as an example, the hardness can reach HV1300-1500, and the temperature of CrC products can reach 800 degrees Celsius.
Metal alloy powder, Pure Metal and Spray Wire products have more applications in glass mold, steel and machinery industries. And XTC products are now become more and more popular in Metal spray coating and thermal spray coating industry.
Coating Service,Metal Spray Coating,Flame Spray Coating,Thermal Spray Coating
Luoyang Golden Egret Geotools Co., Ltd , https://www.xtclasercladding.com