Reactive injection molding (RIM) is an injection molding process utilized for thermosetting compound processing operation, in which the molding compounds undergo cure reactives to form a three dimensional network structure part. Thermosetting molding compound was discovered by Dr. Leo H. Baekeland in 1907. An earlier closed mold technique for processing thermosetting molding compound was the transfer molding process invented by L. E. Shaw in 1926, and followed by a succession of new molding press designs like plunger transfer process.
Currently, screw injection and plunger injection molding machines are wildly applied for molded thermosetting polymers. Rheological (flow) properties and curing reactive of resin system are time and temperature dependent, and extremely determine the end product utility for a particular application. Due to the complicated dynamics of reactive polymer processes coupled with flow behavior, performance requirements of product expected by product designer are not easily acquired by process control; so that, a CAE application, as illustrated in figure 1, implanted with accurate chemorheological models can greatly help part designer to determine whether the selected molding compound meet the manufacturing and end-use properties.
Fig. 1 Â The Simulation of a 75 % filled front spoiler corresponds well with the real part.
[Kunststoffe international 5/2010, Carl Hanser Verlag, Munich.]
Reactive injection molding module featured in Moldex3D R11 provides a new solution in determining the complicated filling behavior which couples the rheological properties and chemical reactive. Moreover, Moldex3D RIM adopts realistic 3D mold filling analysis of the curing rate of thermosets and flow pattern; welding line, air trap, conversion rate, velocity vectors and transfer pressure are also available.
A kinetics model of curing, especially for rubber, is supported. Â The incubation phase is described by the so-called scorch-index for user to determine vulcanization when the cavity is completely filled. Scorch-index predicts probable scorch sections during filling stage. After the scorch index reaches the value 1, the kinetics governed by curing reactive starts. In order to avoid scorch, a suitable injection time let the predicted scorch index smaller than 1 is required. A lower injection time generally leads to a smaller scorch index. In addition, the interactive relation between curing and part insert shift like wire-sweep phenomena in microchip encapsulation, shown in figure 2 and figure 3, can be easily revealed from Moldex3D RIM analysis.
For more information regarding reactive injection molding, please go to our website to learn about our exciting new simulation technology.
         Â
                 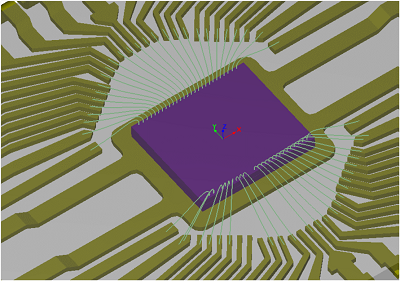
Fig. 2  Distribution of iso-surfaces of melt front inside cavity      Fig. 3  Close up of wire bonding region
Commercial & Industrial Ess,Industrial Storage System,Energy Storage System,Commercial Energy Storage System
Beiamp New Energy Co., Ltd. , https://www.beiamp.net