Abstract: With the rapid development of high-speed railways, on the high-speed railway lines with a speed of over 350km/h, the problem of speed positioning of trains becomes more and more important. This article mainly introduces the application of sensors in high-speed railway speed measurement and positioning technology for everyone to understand.
1. Introduction With the rapid development of high-speed railways, on the high-speed railway lines with a speed of over 350km/h, the problem of speed positioning of trains becomes more and more important. The traditional track circuit positioning method is difficult to meet the positioning requirements of high-speed trains due to the rough positioning and insufficient precision and the inability to detect the instantaneous speed of the train. There is also a method of using the motor to implement the speed positioning method. This method is only applicable to the lines with lower running speed of the train. Speed ​​measurement and positioning can also directly obtain the position and speed information of the train by adding the input signal. However, the measurement accuracy of this method is restricted by some factors, and there are limitations in the cost performance. Sensors in the high-speed railway speed measurement and positioning technology has become the current mainstream products, a wide range of applications, there are many types: pulse speed sensor, inertial acceleration sensor, relative sensor, ground sensor, absolute sensor and so on.
2, the train speed 2.1 wheel shaft speed sensor speed sensor rotation speed sensor of many types, there are magnetoelectric, photoelectric, centrifugal, Hall-type speed sensors. Among them, the wheel axis pulse speed sensor is widely used in high-speed railways. The basic working principle of the wheel axis pulse speed sensor speed measurement is to use the circumference of the wheel as the “ruler†to measure the distance traveled by the train, and to measure the running speed of the train according to the measured distance. The basic formula is:
V=Ï€Dn/3.6
In the formula, π = 3.14, D is the wheel diameter, and n is the wheel speed.
From the above equation, it can be seen that measuring the train speed is to detect the train wheel speed and the column wheel diameter. The pulse speed sensor is mounted on the axle. Every rotation of the axle, the sensor outputs a certain number of pulses, so that the pulse frequency is proportional to the axle speed. The output pulse is directly input into the computer CPU for frequency measurement after isolation and shaping, and then converted to obtain the vehicle speed and travel distance. Its block diagram is shown in Figure 1.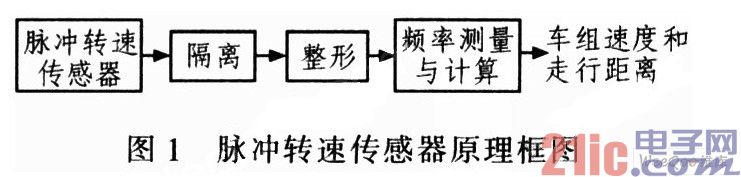
2.2 Inertial Acceleration Sensor The acceleration sensor is an electronic device that can measure acceleration force. Acceleration force is the force acting on an object during acceleration. It can be constant or variable. The general acceleration sensor works according to the principle of piezoelectric effect. The accelerometer uses its internal crystal deformation due to acceleration to generate a voltage. As long as the relationship between the generated voltage and the applied acceleration is calculated, the acceleration can be converted into a voltage output. There are many other ways to make acceleration sensors, such as capacitive effect, thermal bubble effect, and light effect. However, the most basic principle is that the acceleration causes a certain medium to be deformed, and its deformation amount is measured and converted into a voltage output by an associated circuit.
Axis pulse speed sensor also has certain defects: that the wheel idle or slip will cause the train speed measurement error exists, in order to solve such problems, install an acceleration sensor on the train axle, with pulse speed sensor used. The working principle of this method: During the slippage of the train, the internal acceleration of the locomotive is used as the information source of the speed measurement. This information is not related to the status of the wheel rotation and other information, and the wheel shaft pulse sensor is still used for speed measurement during the rest of the working time, so this method is called Speed ​​measurement based on inertial acceleration sensor. When the wheel slips, the acceleration sensor measures the acceleration and the tilt component of the acceleration before the wheel slips, and calculates the train running acceleration when the wheel slips, and then integrates the value to obtain the train running speed in real time when the wheel slips. The specific principle is shown in Figure 2.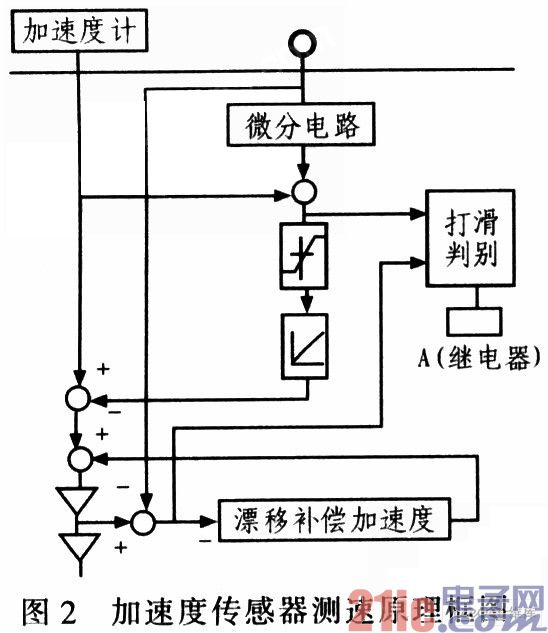
3. Train positioning During the operation of high-speed trains, whether or not it can accurately and timely obtain the train position information is the guarantee for the safe and effective operation of the train.
3.1 Relative Sensors A relative sensor is a device that is installed based on predetermined or previously measured distances, locations, and other information. This method is currently implemented by axle sensors. Its working principle: the pulse frequency signal proportional to the output frequency of the sensor and the wheel shaft speed, through the series of frequency conversion to obtain the speed first, and then integrate the speed and time to obtain the distance.
3.2 Ground sensor The relative sensor must first determine its absolute position and orientation with respect to the earth during operation. To this end, ground sensors must be installed at appropriate locations on the ground, commonly known as beacons. When the locomotive passes, the on-board sensor receives the absolute position information provided by the ground sensor, so that the train updates the distance information and obtains a new initial position, thereby overcoming the relative sensor error error.
3.3 Absolute Sensor Due to the limitations of the relative sensor operation, the absolute sensor becomes the mainstream technology for train positioning in the future high-speed railway operation. Absolute sensors can provide absolute position and orientation information directly, thus realizing the distance measurement of the train.
4. Concluding remarks Through the above discussion, it is shown that the use of sensors for speed measurement and positioning is simple, economical and practical. The measurement data error is in the same range. The sensor is widely used in high-speed railways and is currently the leading product for application. The existing GPS mobile communication and satellite positioning technology methods achieve speed measurement and positioning by directly obtaining the position and speed information of the train by adding an input signal. However, the measurement accuracy of this method is restricted by some factors and has not been promoted for the time being. However, with its mature technology, the application prospects of mobile communications and satellite positioning in high-speed railway will be even broader.
1. Introduction With the rapid development of high-speed railways, on the high-speed railway lines with a speed of over 350km/h, the problem of speed positioning of trains becomes more and more important. The traditional track circuit positioning method is difficult to meet the positioning requirements of high-speed trains due to the rough positioning and insufficient precision and the inability to detect the instantaneous speed of the train. There is also a method of using the motor to implement the speed positioning method. This method is only applicable to the lines with lower running speed of the train. Speed ​​measurement and positioning can also directly obtain the position and speed information of the train by adding the input signal. However, the measurement accuracy of this method is restricted by some factors, and there are limitations in the cost performance. Sensors in the high-speed railway speed measurement and positioning technology has become the current mainstream products, a wide range of applications, there are many types: pulse speed sensor, inertial acceleration sensor, relative sensor, ground sensor, absolute sensor and so on.
2, the train speed 2.1 wheel shaft speed sensor speed sensor rotation speed sensor of many types, there are magnetoelectric, photoelectric, centrifugal, Hall-type speed sensors. Among them, the wheel axis pulse speed sensor is widely used in high-speed railways. The basic working principle of the wheel axis pulse speed sensor speed measurement is to use the circumference of the wheel as the “ruler†to measure the distance traveled by the train, and to measure the running speed of the train according to the measured distance. The basic formula is:
V=Ï€Dn/3.6
In the formula, π = 3.14, D is the wheel diameter, and n is the wheel speed.
From the above equation, it can be seen that measuring the train speed is to detect the train wheel speed and the column wheel diameter. The pulse speed sensor is mounted on the axle. Every rotation of the axle, the sensor outputs a certain number of pulses, so that the pulse frequency is proportional to the axle speed. The output pulse is directly input into the computer CPU for frequency measurement after isolation and shaping, and then converted to obtain the vehicle speed and travel distance. Its block diagram is shown in Figure 1.
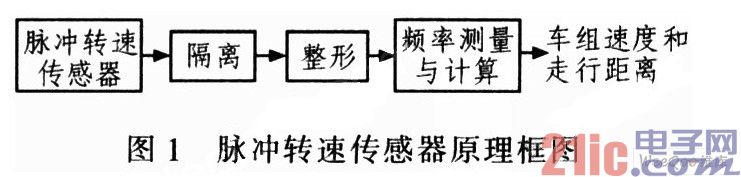
2.2 Inertial Acceleration Sensor The acceleration sensor is an electronic device that can measure acceleration force. Acceleration force is the force acting on an object during acceleration. It can be constant or variable. The general acceleration sensor works according to the principle of piezoelectric effect. The accelerometer uses its internal crystal deformation due to acceleration to generate a voltage. As long as the relationship between the generated voltage and the applied acceleration is calculated, the acceleration can be converted into a voltage output. There are many other ways to make acceleration sensors, such as capacitive effect, thermal bubble effect, and light effect. However, the most basic principle is that the acceleration causes a certain medium to be deformed, and its deformation amount is measured and converted into a voltage output by an associated circuit.
Axis pulse speed sensor also has certain defects: that the wheel idle or slip will cause the train speed measurement error exists, in order to solve such problems, install an acceleration sensor on the train axle, with pulse speed sensor used. The working principle of this method: During the slippage of the train, the internal acceleration of the locomotive is used as the information source of the speed measurement. This information is not related to the status of the wheel rotation and other information, and the wheel shaft pulse sensor is still used for speed measurement during the rest of the working time, so this method is called Speed ​​measurement based on inertial acceleration sensor. When the wheel slips, the acceleration sensor measures the acceleration and the tilt component of the acceleration before the wheel slips, and calculates the train running acceleration when the wheel slips, and then integrates the value to obtain the train running speed in real time when the wheel slips. The specific principle is shown in Figure 2.
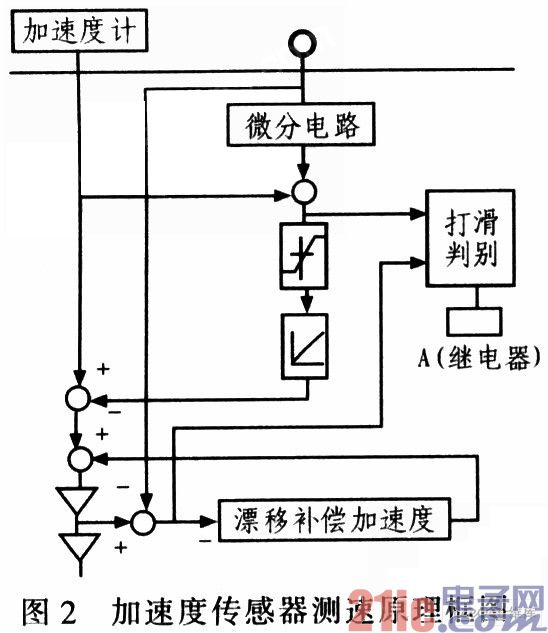
3. Train positioning During the operation of high-speed trains, whether or not it can accurately and timely obtain the train position information is the guarantee for the safe and effective operation of the train.
3.1 Relative Sensors A relative sensor is a device that is installed based on predetermined or previously measured distances, locations, and other information. This method is currently implemented by axle sensors. Its working principle: the pulse frequency signal proportional to the output frequency of the sensor and the wheel shaft speed, through the series of frequency conversion to obtain the speed first, and then integrate the speed and time to obtain the distance.
3.2 Ground sensor The relative sensor must first determine its absolute position and orientation with respect to the earth during operation. To this end, ground sensors must be installed at appropriate locations on the ground, commonly known as beacons. When the locomotive passes, the on-board sensor receives the absolute position information provided by the ground sensor, so that the train updates the distance information and obtains a new initial position, thereby overcoming the relative sensor error error.
3.3 Absolute Sensor Due to the limitations of the relative sensor operation, the absolute sensor becomes the mainstream technology for train positioning in the future high-speed railway operation. Absolute sensors can provide absolute position and orientation information directly, thus realizing the distance measurement of the train.
4. Concluding remarks Through the above discussion, it is shown that the use of sensors for speed measurement and positioning is simple, economical and practical. The measurement data error is in the same range. The sensor is widely used in high-speed railways and is currently the leading product for application. The existing GPS mobile communication and satellite positioning technology methods achieve speed measurement and positioning by directly obtaining the position and speed information of the train by adding an input signal. However, the measurement accuracy of this method is restricted by some factors and has not been promoted for the time being. However, with its mature technology, the application prospects of mobile communications and satellite positioning in high-speed railway will be even broader.
A Linear Actuator is an actuator that creates motion in a straight line. Pneumatic Linear Actuators, Compressed Air Linear Actuators, Pneumatic Round Cylinders are used in machine tools and industrial machinery, in computer peripherals such as disk drives and printers, in valves and dampers, and in many other places where linear motion is required.
Shengfei manufactures cylinders to meet ISO standards, SMC Series cylinders.
Linear Actuator
Linear Actuator,Electric Linear Actuator,Electric Actuator
Ningbo Precise Smart Equipment CO.,LTD , http://www.shengfeipneumatic.com