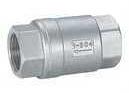
1. Leakage Under the normal operating pressure of the device, leakage beyond the allowable level occurs between the disc and the sealing surface of the valve seat. The reasons are: There is dirt between the valve flap and the sealing surface of the valve seat. Use a lifting wrench to open the valve a few times to flush away the dirt; the sealing surface is damaged. Should be based on the degree of damage, grinding or grinding after grinding method to repair; valve stem bending, tilting or deflection of the lever and fulcrum, so that the spool and valve disc misalignment. Should be reassembled or replaced; spring elasticity reduced or lost elasticity. Replace the spring and readjust the opening pressure.
2. The frequency jump or vibration of the valve is mainly due to the too high spring stiffness. Should use a spring with appropriate stiffness; improper adjustment of the adjustment ring will make the pressure in the seat back too high. The position of the adjusting ring should be readjusted; the discharge pipe resistance is too large, resulting in excessive discharge back pressure. The discharge pipe resistance should be reduced.
3. The reason why this condition is not turned on when the pressure is set is that constant pressure is not allowed. The amount of spring compression or the position of the weight should be readjusted; the valve flap sticks to the valve seat. The safety valve shall be manually deflated or drained periodically; the leverage of the lever-type safety valve is jammed or the hammer is moved. The weight position should be readjusted and the lever should move freely.
4. The disc is not returned to the seat after discharge. This is mainly caused by the spring bending of the valve stem, the improper installation position of the valve disc, or being stuck. Should be re-assembled.
5. After the exhaust pressure continues to rise This is mainly because of the safety valve discharge capacity of small flat equipment safety, should be re-select the appropriate safety valve; stem center line is not correct or spring rust, so that the valve flap can not be opened to due The height should be re-assembled valve stem or replace the spring; exhaust pipe cut enough, should be taken to meet the safety discharge area of ​​the exhaust pipe.
6. Less than the specified pressure opening is mainly constant pressure is not allowed; spring aging elasticity decreased. Tighten the adjusting screw or replace the spring properly.
Protective Film,PVC Adhesive Film,Camera Special Film
Fenghua Jade Motor Co., Ltd. , http://www.nstape.com