Thermal imaging cameras are suitable for non-contact temperature measurement projects of all companies worldwide. The spot temperature meter is another widely used non-contact temperature measurement tool in industrial applications. It works in the same way as a thermal imager: it detects infrared radiation and converts it into a temperature reading. However, compared to spot thermometers, infrared cameras have several advantages:
â— The thermometer only shows numbers and the infrared camera can generate images.
â— The spot thermometer can only read the temperature of a single point, and the infrared camera displays the temperature readings of all pixels in the thermal image.
â— Due to the advanced optical lens, the infrared camera can detect temperature at a longer distance, which helps to inspect large areas.
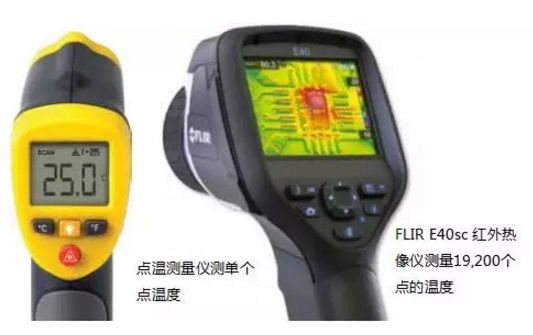
The spot thermometer is also commonly referred to as a spot temperature wood or infrared thermometer. Because its working principle is the same as an infrared thermometer, it can be considered as an infrared camera with only one pixel. This tool can accomplish multiple tasks, but because only a single point of temperature can be measured, operators can miss a lot of critical information, failing to be aware of certain critical components that are about to fail and that are in urgent need of repair.
Use thousands Thermometers Thermometers <br> <br> Similarly, infrared camera can also provide non-contact temperature reading. The difference is that the thermal imager can display thousands of temperature readings at a time and each pixel corresponds to a temperature reading.
An infrared camera is equivalent to thousands of spot thermometers.
The FLIRE40sc thermal imaging camera has a resolution of 160x120 pixels and can read 19200 temperature readings at one time. The FLIRT1050sc is a high-end thermal imaging camera for industrial R&D/scientific applications. Its resolution is 1024x768, and 786,432 temperature readings can be obtained at a time. .
Save Time and Detect Thermal Imagers can not only measure the temperature of thousands of points, but also convert temperature readings into thermal images. The generated thermal image can fully reflect the overall condition of the equipment to be inspected, and the operator can immediately discover the subtle hot spots that the temperature detector cannot easily detect.
In addition, thermal imaging cameras can also save a lot of time, after all, using a spot thermometer to measure a large area with a large number of components is time-consuming and laborious, because each part needs to be scanned separately.
The thermal imager can be used to check the thermal problem of the printed circuit board, complete the quality inspection or check the thermal effects of the automotive industry, or perform error analysis in the laboratory.
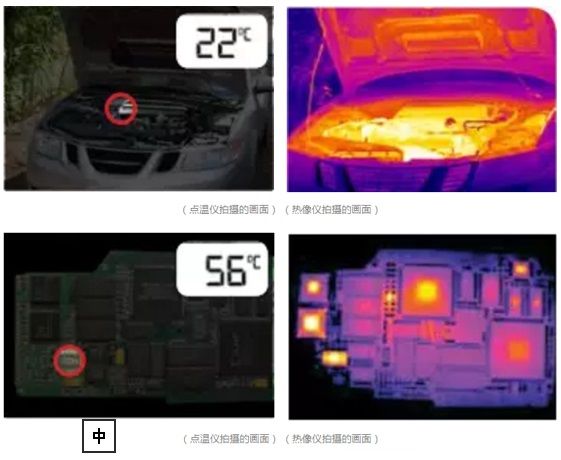
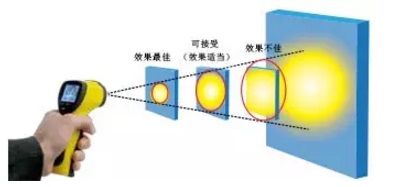
To accurately measure the temperature of an object using a point thermometer, the target object needs to completely cover the light spot. This limits the precise temperature measurement distance.
Another advantage of thermal imaging cameras compared to spot thermometers is the ability to accurately measure the temperature of objects at longer distances. The distance that can measure a given size target is called "distance coefficient ratio" (D:S) or "spot ratio" (SSR). But where does this ratio come from and what does it mean?
The spot size of the spot thermometer is the smallest area where the device can accurately measure the object. This means that the object to be measured (also called the "target") needs to cover the entire spot of light. The infrared radiation emitted by the target is projected onto the detector through the optical lens of the spot thermometer. If the target is smaller than the light spot, the detector may detect radiation around the target object. At this point, the spot temperature meter reads not only the target temperature, but the combined temperature of the target and its surroundings.
According to the properties of the optical lens, the farther the spot thermometer is from the measurement target, the larger the light spot will be. Similarly, the smaller the target, the closer the thermometer should be to the measurement target in order to accurately measure its temperature. Therefore, it is important to pay attention to the spot size to ensure that the measurement point is close enough to the target to cover the entire spot. If it can be a little closer to form a certain safety boundary, the effect will be better.
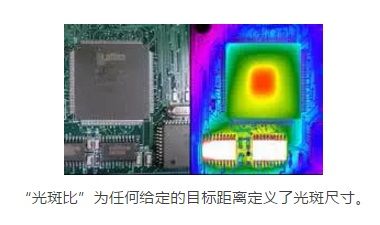
For example, if the spot thermometer's SSR is 1:30, it means that a temperature of 1 cm in diameter can be accurately measured at a distance of 30 cm. The temperature of a spot with a diameter of 4 cm can be accurately measured (1.2 m) at 120 cm. Most point thermometers have an SSR between 1:5 and 1:50. In other words, most spot thermometers can measure a target diameter of 1 cm at 5-50 cm.
The infrared camera is similar to the spot thermometer. Its infrared radiation is projected onto the detector matrix. Each pixel on the image corresponds to a temperature value. Thermal imager manufacturers often do not specify the SSR value when describing the spatial resolution of their products, but rather use spatial resolution (IFOV). IFOV refers to the angle of view of a single pixel of the thermal imager detector array.
In theory, IFOV directly determines the spot ratio of the thermal imager. When the infrared radiation emitted by the target passes through the optical lens and then is projected onto the detector, the projected infrared radiation should at least completely cover the pixels of one detector, which corresponds to one pixel of the thermal image. Therefore, theoretically, one pixel of the thermal image should be sufficient to ensure the correct temperature measurement.
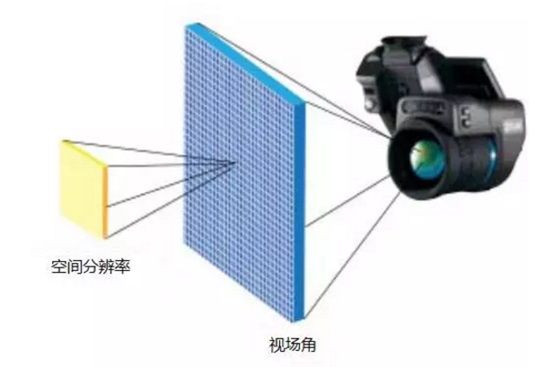
IFOV is usually expressed in milliradians (one thousandth of 1 radian). Arc represents the ratio of arc length to radius. 1 radians mathematically means the angle formed when the arc length is equal to the radius of the circle. Since the circumference of the circle is C=2πr (r is the radius), 1 radians equals 1/(2π) of the circumference, or approximately 57.296°, ie 1 milliradian of 0.057°.
When using a thermal imager to measure the temperature of a certain target, we assume that the distance from the target is equal to the radius of the circle, while assuming that the target is fairly flat. Since the perspective of a single detector pixel is small, it can be assumed that the tangent of the angle is approximately equal to its The radians value.
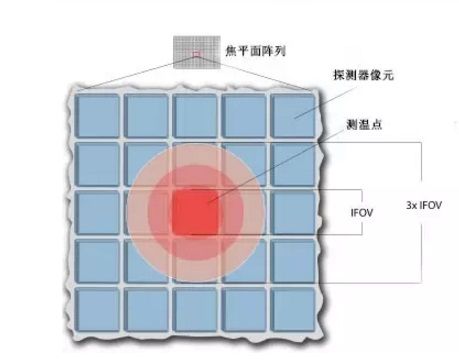
Ideally, the projection target should cover at least one pixel. To ensure accurate readings and explain the dispersion of light during projection, it is recommended to cover a slightly larger area.
In this formula, the units of spot size and target size are expressed in centimeters (cm), and IFOV is expressed in millirads (mrad). When the distance is 100 cm and IFOV is 1 mrad, the spot size is 0.1 cm. If the spot size of 0.1 cm can be measured at 100 cm, the spot size of 1 cm can be measured at 1000 cm, which means that the distance coefficient ratio is 1:1000.
If we substituting the above calculation into the formula, the SSR is expressed as a 1:X form, with 1 representing the spot size and X representing the distance, then the formula for X is as follows
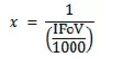
Where IFOV is expressed in millirads (mrad).
The ideal and actual optical lens can use the above formula to calculate a thermal imager with an IFOV of 1.4 mrad. The theoretical SSR is 1:714. Therefore, it is theoretically possible to measure a diameter of 1 cm at a distance of 7 m. Projecting infrared radiation into the lens of the detector can cause dispersion and other optical anomalies and cannot ensure that the target can be accurately projected onto a single detector cell.
Projected infrared radiation may also come from neighboring detector pixels. In other words: The surface temperature around the target may affect the temperature reading.
As with a spot thermometer, the target should not only completely cover the light spot but also cover the safety margin near the light spot. When using an infrared detector thermal imager to measure the temperature, it is recommended to use a safety margin. The safety margin is obtained from the measured field of view (MFOV). The MFOV describes the actual measuring spot size of the camera, in other words, the minimum measurement area for obtaining correct readings.
MFOV is usually represented by many IFOVs (field of view of a single pixel). The common practice of infrared detector thermal imager is: In view of optical anomalies, the target needs to cover at least 3 times the area of ​​IFOV. This means that in a thermal image, the target should cover not only one pixel but also its surrounding pixels. Under ideal conditions, the pixel should be sufficient to complete the measurement.
When using this convention, the formula for determining the spot ratio may take into account the coefficients of the real optical lens. To get closer to the true value, you can use 3 times IFOV instead of 1 times IFOV, and the formula is as follows:
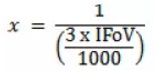
Where IFOV is expressed in millirads (mrad).
Based on this formula, the thermal imager SSR of 1.4 mrad for IFOV is 1:238, which means that a diameter of 1 cm can be measured at 2.4 m. Due to the existence of safety boundaries, theoretical values ​​may tend to be conservative. The true SSR may be higher, but using these conservative SSR values ​​ensures the accuracy of the temperature readings.
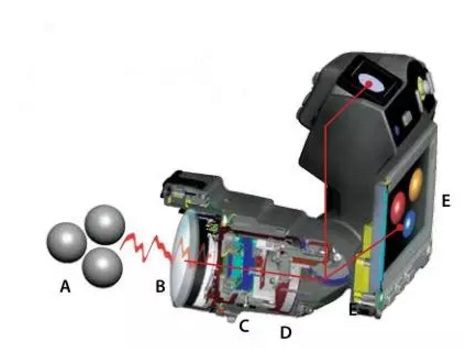
The infrared energy (A) from the object is focused by the optical lens (B) and projected onto the infrared detector (C). The detector sends information to the sensor electronics (D) for image processing. The electronics convert the data from the detector into an image (E) that can be read on the viewfinder, standard video display, or LCD display.
The spot thermometer's SSR value is usually between 1:5 and 1:50. Most affordable models have an SSR value between 1:5 and 1:10. The more advanced the feature, the higher the price, and the SSR value can be as high as 1:40 or even 1:50. Note: When it comes to optical lenses, the same problem exists with the spot thermometer and the infrared camera. When comparing the temperature gauge's technical specifications, it must be clear whether the SSR value is the theoretical value or the compensation value to the lens.
Detecting a temperature at a long distance <br> <br> even taking into account the actual coefficient over the optical lens, in measuring distance, with the thermal imager Thermometers are also considerable differences. When the measurement target is 1cm, most spot thermometers have a distance of 10-50cm and it is difficult to exceed this range.
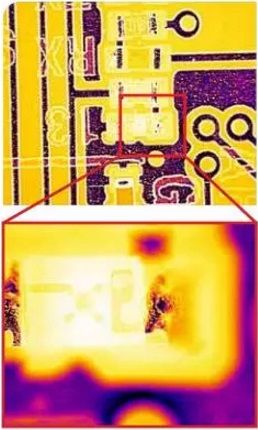
Close-up with the microscope head can take detailed image details for easy measurement of tiny hot spots. For point thermometers, this is extremely difficult. The top image was taken with a 4x close-up shot and the bottom image was taken with a 15μm lens.
For cameras of the same size, the camera can precisely measure its target at a distance of several meters. The FLIRE40 thermal imaging camera with an IFOV of 2.72mrad can still measure temperature at a distance of 120cm and measure a temperature of 1cm. The FLIRT1050sc is a FLIR high-end industrial thermal imaging camera that uses a standard 28° lens to measure targets of the same size at a distance of 7m.
These values ​​can be calculated using standard lenses. Many advanced cameras have interchangeable lenses. When using different lenses, the IFOV will also change, which in turn will affect the spot ratio. For the FLIRT1050sc thermal imaging camera, the FLIR not only provides a standard 28° lens, it also offers a 12° telephoto lens. With a lens specifically designed for distance viewing, the spot ratio will be greater. With a 12° telephoto lens, the FLIRT1050sc infrared camera has an IFOV of 0.20 mrad. With this lens, the same camera can accurately measure targets of the same size at a distance of 17m.
Judging if it is necessary to approach the target further, the performance of the infrared camera is obviously higher than that of the spot thermometer, but the SSR value only refers to the distance that can accurately measure the temperature. In actual testing, hot spots do not require accurate temperature readings. In a thermal image, hot spots are still legible even when the target covers only one pixel. The temperature reading may not be perfect, but it can be used to detect hot spots, the operator can be closer to the target, to ensure that the target can cover more pixels in the thermal image, to ensure accurate temperature readings.
When measuring tiny targets, the spot thermometer also faces great challenges. This feature has become increasingly important in the detection of electronic components. As the processing speed of the equipment continues to increase and it needs to be installed in a smaller volume space, finding a way to dissipate heat and identify hot spots is a very practical problem. The spot thermometer can effectively detect and measure the temperature, but its spot size is too large. However, the focal length per pixel spot size of thermal imagers equipped with close-up lenses can be adjusted as low as 5 μm, allowing engineers and technicians to measure subtle targets.
Eliminating guesswork and seeing the truth The thermometer can only display one reading and the reading may not be accurate, making it easy to guess. The infrared camera can accurately display the heat, not only can realize the temperature measurement, but also can display the transient image of the temperature distribution. The perfect combination of visible light information and accurate temperature measurement helps to quickly and accurately find fault points. Instantly upgraded to FLIR Systems' thermal imaging camera to find problems in a faster and more convenient way to eliminate all kinds of guesswork due to uncertainty. (end)
â— The thermometer only shows numbers and the infrared camera can generate images.
â— The spot thermometer can only read the temperature of a single point, and the infrared camera displays the temperature readings of all pixels in the thermal image.
â— Due to the advanced optical lens, the infrared camera can detect temperature at a longer distance, which helps to inspect large areas.
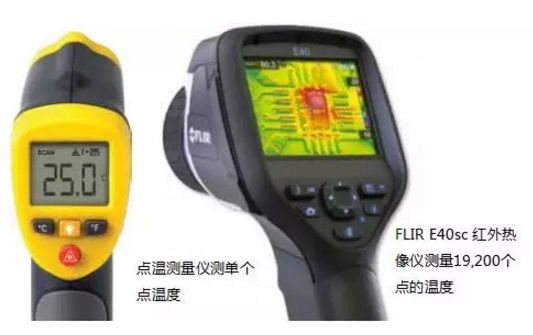
The spot thermometer is also commonly referred to as a spot temperature wood or infrared thermometer. Because its working principle is the same as an infrared thermometer, it can be considered as an infrared camera with only one pixel. This tool can accomplish multiple tasks, but because only a single point of temperature can be measured, operators can miss a lot of critical information, failing to be aware of certain critical components that are about to fail and that are in urgent need of repair.
Use thousands Thermometers Thermometers <br> <br> Similarly, infrared camera can also provide non-contact temperature reading. The difference is that the thermal imager can display thousands of temperature readings at a time and each pixel corresponds to a temperature reading.
An infrared camera is equivalent to thousands of spot thermometers.
The FLIRE40sc thermal imaging camera has a resolution of 160x120 pixels and can read 19200 temperature readings at one time. The FLIRT1050sc is a high-end thermal imaging camera for industrial R&D/scientific applications. Its resolution is 1024x768, and 786,432 temperature readings can be obtained at a time. .
Save Time and Detect Thermal Imagers can not only measure the temperature of thousands of points, but also convert temperature readings into thermal images. The generated thermal image can fully reflect the overall condition of the equipment to be inspected, and the operator can immediately discover the subtle hot spots that the temperature detector cannot easily detect.
In addition, thermal imaging cameras can also save a lot of time, after all, using a spot thermometer to measure a large area with a large number of components is time-consuming and laborious, because each part needs to be scanned separately.
The thermal imager can be used to check the thermal problem of the printed circuit board, complete the quality inspection or check the thermal effects of the automotive industry, or perform error analysis in the laboratory.
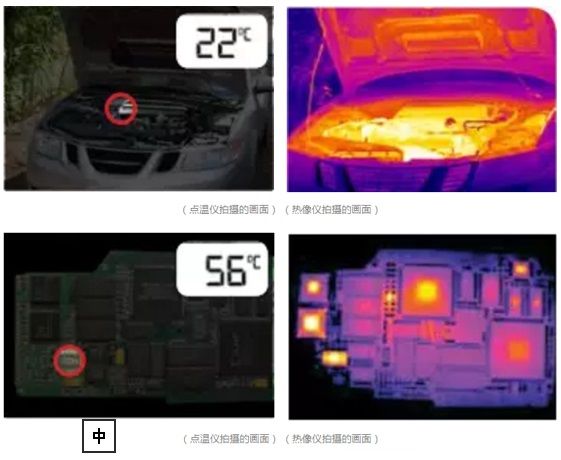
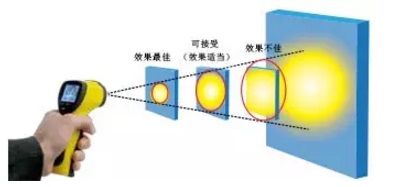
To accurately measure the temperature of an object using a point thermometer, the target object needs to completely cover the light spot. This limits the precise temperature measurement distance.
Another advantage of thermal imaging cameras compared to spot thermometers is the ability to accurately measure the temperature of objects at longer distances. The distance that can measure a given size target is called "distance coefficient ratio" (D:S) or "spot ratio" (SSR). But where does this ratio come from and what does it mean?
The spot size of the spot thermometer is the smallest area where the device can accurately measure the object. This means that the object to be measured (also called the "target") needs to cover the entire spot of light. The infrared radiation emitted by the target is projected onto the detector through the optical lens of the spot thermometer. If the target is smaller than the light spot, the detector may detect radiation around the target object. At this point, the spot temperature meter reads not only the target temperature, but the combined temperature of the target and its surroundings.
According to the properties of the optical lens, the farther the spot thermometer is from the measurement target, the larger the light spot will be. Similarly, the smaller the target, the closer the thermometer should be to the measurement target in order to accurately measure its temperature. Therefore, it is important to pay attention to the spot size to ensure that the measurement point is close enough to the target to cover the entire spot. If it can be a little closer to form a certain safety boundary, the effect will be better.
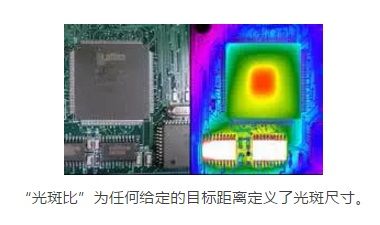
For example, if the spot thermometer's SSR is 1:30, it means that a temperature of 1 cm in diameter can be accurately measured at a distance of 30 cm. The temperature of a spot with a diameter of 4 cm can be accurately measured (1.2 m) at 120 cm. Most point thermometers have an SSR between 1:5 and 1:50. In other words, most spot thermometers can measure a target diameter of 1 cm at 5-50 cm.
The infrared camera is similar to the spot thermometer. Its infrared radiation is projected onto the detector matrix. Each pixel on the image corresponds to a temperature value. Thermal imager manufacturers often do not specify the SSR value when describing the spatial resolution of their products, but rather use spatial resolution (IFOV). IFOV refers to the angle of view of a single pixel of the thermal imager detector array.
In theory, IFOV directly determines the spot ratio of the thermal imager. When the infrared radiation emitted by the target passes through the optical lens and then is projected onto the detector, the projected infrared radiation should at least completely cover the pixels of one detector, which corresponds to one pixel of the thermal image. Therefore, theoretically, one pixel of the thermal image should be sufficient to ensure the correct temperature measurement.
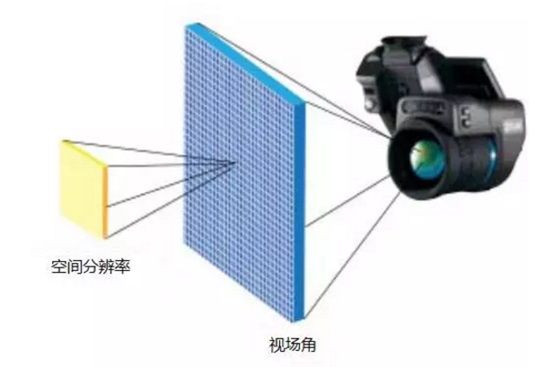
IFOV is usually expressed in milliradians (one thousandth of 1 radian). Arc represents the ratio of arc length to radius. 1 radians mathematically means the angle formed when the arc length is equal to the radius of the circle. Since the circumference of the circle is C=2πr (r is the radius), 1 radians equals 1/(2π) of the circumference, or approximately 57.296°, ie 1 milliradian of 0.057°.
When using a thermal imager to measure the temperature of a certain target, we assume that the distance from the target is equal to the radius of the circle, while assuming that the target is fairly flat. Since the perspective of a single detector pixel is small, it can be assumed that the tangent of the angle is approximately equal to its The radians value.
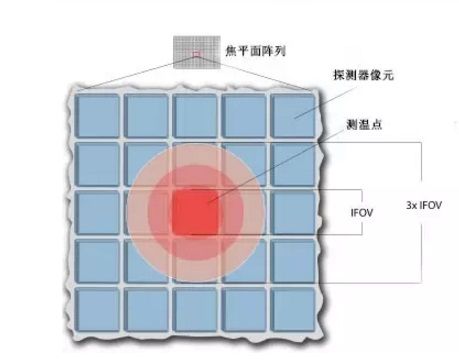
Ideally, the projection target should cover at least one pixel. To ensure accurate readings and explain the dispersion of light during projection, it is recommended to cover a slightly larger area.
In this formula, the units of spot size and target size are expressed in centimeters (cm), and IFOV is expressed in millirads (mrad). When the distance is 100 cm and IFOV is 1 mrad, the spot size is 0.1 cm. If the spot size of 0.1 cm can be measured at 100 cm, the spot size of 1 cm can be measured at 1000 cm, which means that the distance coefficient ratio is 1:1000.
If we substituting the above calculation into the formula, the SSR is expressed as a 1:X form, with 1 representing the spot size and X representing the distance, then the formula for X is as follows
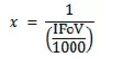
Where IFOV is expressed in millirads (mrad).
The ideal and actual optical lens can use the above formula to calculate a thermal imager with an IFOV of 1.4 mrad. The theoretical SSR is 1:714. Therefore, it is theoretically possible to measure a diameter of 1 cm at a distance of 7 m. Projecting infrared radiation into the lens of the detector can cause dispersion and other optical anomalies and cannot ensure that the target can be accurately projected onto a single detector cell.
Projected infrared radiation may also come from neighboring detector pixels. In other words: The surface temperature around the target may affect the temperature reading.
As with a spot thermometer, the target should not only completely cover the light spot but also cover the safety margin near the light spot. When using an infrared detector thermal imager to measure the temperature, it is recommended to use a safety margin. The safety margin is obtained from the measured field of view (MFOV). The MFOV describes the actual measuring spot size of the camera, in other words, the minimum measurement area for obtaining correct readings.
MFOV is usually represented by many IFOVs (field of view of a single pixel). The common practice of infrared detector thermal imager is: In view of optical anomalies, the target needs to cover at least 3 times the area of ​​IFOV. This means that in a thermal image, the target should cover not only one pixel but also its surrounding pixels. Under ideal conditions, the pixel should be sufficient to complete the measurement.
When using this convention, the formula for determining the spot ratio may take into account the coefficients of the real optical lens. To get closer to the true value, you can use 3 times IFOV instead of 1 times IFOV, and the formula is as follows:
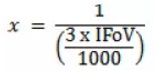
Where IFOV is expressed in millirads (mrad).
Based on this formula, the thermal imager SSR of 1.4 mrad for IFOV is 1:238, which means that a diameter of 1 cm can be measured at 2.4 m. Due to the existence of safety boundaries, theoretical values ​​may tend to be conservative. The true SSR may be higher, but using these conservative SSR values ​​ensures the accuracy of the temperature readings.
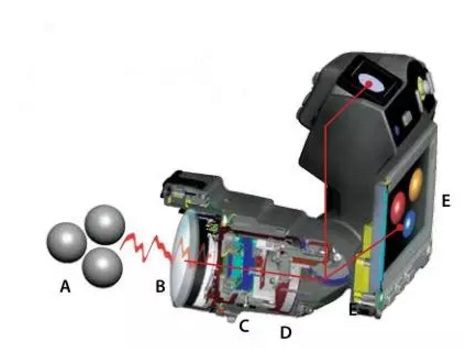
The infrared energy (A) from the object is focused by the optical lens (B) and projected onto the infrared detector (C). The detector sends information to the sensor electronics (D) for image processing. The electronics convert the data from the detector into an image (E) that can be read on the viewfinder, standard video display, or LCD display.
The spot thermometer's SSR value is usually between 1:5 and 1:50. Most affordable models have an SSR value between 1:5 and 1:10. The more advanced the feature, the higher the price, and the SSR value can be as high as 1:40 or even 1:50. Note: When it comes to optical lenses, the same problem exists with the spot thermometer and the infrared camera. When comparing the temperature gauge's technical specifications, it must be clear whether the SSR value is the theoretical value or the compensation value to the lens.
Detecting a temperature at a long distance <br> <br> even taking into account the actual coefficient over the optical lens, in measuring distance, with the thermal imager Thermometers are also considerable differences. When the measurement target is 1cm, most spot thermometers have a distance of 10-50cm and it is difficult to exceed this range.
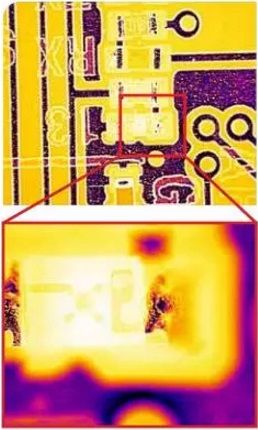
Close-up with the microscope head can take detailed image details for easy measurement of tiny hot spots. For point thermometers, this is extremely difficult. The top image was taken with a 4x close-up shot and the bottom image was taken with a 15μm lens.
For cameras of the same size, the camera can precisely measure its target at a distance of several meters. The FLIRE40 thermal imaging camera with an IFOV of 2.72mrad can still measure temperature at a distance of 120cm and measure a temperature of 1cm. The FLIRT1050sc is a FLIR high-end industrial thermal imaging camera that uses a standard 28° lens to measure targets of the same size at a distance of 7m.
These values ​​can be calculated using standard lenses. Many advanced cameras have interchangeable lenses. When using different lenses, the IFOV will also change, which in turn will affect the spot ratio. For the FLIRT1050sc thermal imaging camera, the FLIR not only provides a standard 28° lens, it also offers a 12° telephoto lens. With a lens specifically designed for distance viewing, the spot ratio will be greater. With a 12° telephoto lens, the FLIRT1050sc infrared camera has an IFOV of 0.20 mrad. With this lens, the same camera can accurately measure targets of the same size at a distance of 17m.
Judging if it is necessary to approach the target further, the performance of the infrared camera is obviously higher than that of the spot thermometer, but the SSR value only refers to the distance that can accurately measure the temperature. In actual testing, hot spots do not require accurate temperature readings. In a thermal image, hot spots are still legible even when the target covers only one pixel. The temperature reading may not be perfect, but it can be used to detect hot spots, the operator can be closer to the target, to ensure that the target can cover more pixels in the thermal image, to ensure accurate temperature readings.
When measuring tiny targets, the spot thermometer also faces great challenges. This feature has become increasingly important in the detection of electronic components. As the processing speed of the equipment continues to increase and it needs to be installed in a smaller volume space, finding a way to dissipate heat and identify hot spots is a very practical problem. The spot thermometer can effectively detect and measure the temperature, but its spot size is too large. However, the focal length per pixel spot size of thermal imagers equipped with close-up lenses can be adjusted as low as 5 μm, allowing engineers and technicians to measure subtle targets.
Eliminating guesswork and seeing the truth The thermometer can only display one reading and the reading may not be accurate, making it easy to guess. The infrared camera can accurately display the heat, not only can realize the temperature measurement, but also can display the transient image of the temperature distribution. The perfect combination of visible light information and accurate temperature measurement helps to quickly and accurately find fault points. Instantly upgraded to FLIR Systems' thermal imaging camera to find problems in a faster and more convenient way to eliminate all kinds of guesswork due to uncertainty. (end)
Irregular Foam Roller,Soreness Release Foam Rollers,Fitness Yoga Foam Roller,Eva Yoga Foam Roller
Jiangsu Laiao Material Technology Co., Ltd. , https://www.jslaiao.com