High-end market space PVB is widely used as a sandwich main material for safety glass due to its excellent adhesion and optical properties. The low-end products are used for building safety glass, and high-end products are used as bullet-proof glass for aircrafts, tanks, and warships in the military industry, and are also widely used in automobile windshields. In recent years, due to the vigorous development of the automotive, aerospace and marine industries, the high-end PVB has brought about a huge market capacity, and domestic high-end PVBs have also begun to develop under the impetus of the market.
The automotive industry is an important market for high-end PVBs. In the automotive industry, PVB is the main material for the manufacture of automotive windshields. In recent years, the growth drivers of the global automotive industry have mainly come from China, India, and Latin America. The rapid growth of the Chinese automotive market has contributed most prominently to the world. According to statistics, China's auto market has maintained rapid growth for six consecutive years. From 2001 to 2006, China's auto production increased by an average of 25.8%. In 2007, the domestic passenger car production capacity has reached 9.17 million. Liu Ming, chief researcher and director of the market research department of the National Information Center Economic Consulting Center, said: “The automobile market will continue to maintain a relatively high growth rate in 2008, and the growth rate of passenger vehicles will remain at 20%.†However, according to the reporter's understanding, China's auto glass is all dependent on imports, and it is not necessary to replace domestic imports of high-end PVB products.
In addition, PVBs produced with special formulae have also been widely used in aerospace, military and high-tech fields. Such as used in aircraft, spacecraft, military equipment, solar cells and solar receivers, etc., applied in the field of industrial composite damping steel plate.
With the development of China's automotive and aerospace industries, high-end PVB has potential huge market demand.
According to industry experts, domestic demand for PVB is about 40,000 tons per year, which is increasing at a rate of 10% per year, while domestic production is only 13,000 tons per year, and all of them are ordinary products.
Poor quality of domestic products According to reports, when it came to PVB projects, some companies only made quick profits, invested less, and built production lines with low technical content and low quality standards. These equipment can only eat the corners of recycled materials, can not use resin powder as raw materials, and related product testing equipment is not matched, eventually leading to poor product quality, production cost pressure, lack of market competitiveness.
Compared with similar products of major international companies, there is still a certain gap between the quality of domestic PVBs, and the gap between some technical indicators is still quite large. This is an indisputable fact. The key technologies for PVB production are basically in the hands of large companies such as DuPont, Japan's Sekisui, Kuraray, and Weike.
The annual production capacity of domestic membrane PVB is less than 2,000 tons. At present, only PVBs produced by three companies in Hong Kong Jianye and Wenzhou Great Wall can be used for membranes, but they are mainly used for building safety glass and cannot produce high-end PVBs for automotive safety glass.
Currently, the domestic market is only officially importing more than 1,000 tons of PVB per year, and the unit price is about 50,000 yuan per ton, which is very expensive; direct import of PVB film is about 20,000 tons; the remaining more than 10,000 tons are smuggled into foreign PVB waste, and then proceed Secondary processing, although the price is a little cheaper, the quality of the diaphragms produced after processing is poor, and it has seriously impacted the development of PVB market for domestic high-end membranes.
Chinese companies started to start Industry experts said that China's high-end PVB all rely on imports, mainly due to lack of production processes and supporting materials. Because the PVB production process is PVA (polyvinyl alcohol) aqueous solution under the action of the catalyst and butyraldehyde condensation to polyvinyl butyral, washed with water to dry to become PVB powdered resin. The distribution range of relative molecular mass of foreign PVA is narrow, and the distribution range of domestic PVA relative molecular mass is wide, which affects the stability of PVB product quality. Moreover, China adopts old technology, and companies do not have membrane supporting research institutions, which also results in the high dependence of PVB for high-end membranes One of the reasons.
Mi Renyi, head of the PVB project of Dongguan Baibaishun Petrochemical Co., Ltd., said that Bai Baishun, through cooperation with the Beijing Institute of Plastics, can identify whether the high-end PVB produced by the Beijing Institute of Plastics can be used as a membrane. Research institute.
With the further expansion of the high-end PVB market, several large foreign companies have developed high-tech and high-value PVB membrane high-end new products to further enhance safety, penetration resistance, structural integrity, and solar energy. The properties of control, sound insulation, and UV protection are used to replace some of the old products or explore new market areas to maintain their monopoly position in the international high-end membrane PVB market.
Therefore, in order to continue to survive and develop, domestic PVB manufacturers must invest a certain percentage of human and financial resources to develop other new products in order to reduce the gap with similar foreign companies as soon as possible.
Derrick Hyperpool Shaker Screen
Replacement PMD Screens for Derrick Hyperpool Shakers
SJ-Derrick Hyperpool PMD Shaker Screen is one of the most popular Derrick shaker screens replacement. It is designed for the high capacity Hyperpool 4-panel shale shakers. Installed with pyramid screens, the non-blanked screening area has increased 20% than conventional flat screens. All replacement shaker screens for Derrick shale shakers are all compliant with API RP 13C (ISO 13501), the new industry standard for physical testing and labeling of shaker screens.
Technical Parameter
- Material: stainless steel 304/316/316 L.
- Construction Type: PMD (pyramid).
- Wear Mesh Shape: rectangle.
- API RP 13 C Designation: API 20 – API 325.
- Series: DX, DF, HP optional.
- Color: green.
- Package: 2 pcs per carton, packed in wooden case.
Adaptable Shale Shaker Model
SJ-Derrick Hyperpool PMD Shaker Screen are used as the substitute screen for
- Derrick Hyperpool 4-panel shaker.
- Derrick Triple Hyperpool shaker.
- Derrick Dual Hyperpool with mud cleaner.
- Derrick Hyperpool VE (Vapor Extraction).
Competitive Advantage
- Stainless steel 304/316 wire mesh for longevity.
- Increase shaker capacity and reduce muds loss.
- Non-blanked screening area increased by more than 20%.
- Scientific & reasonable cost control system for competitive price.
- API RP 13C (ISO 13501) compliant.
- Adequate inventory in the shortest time to meet customers' demand.
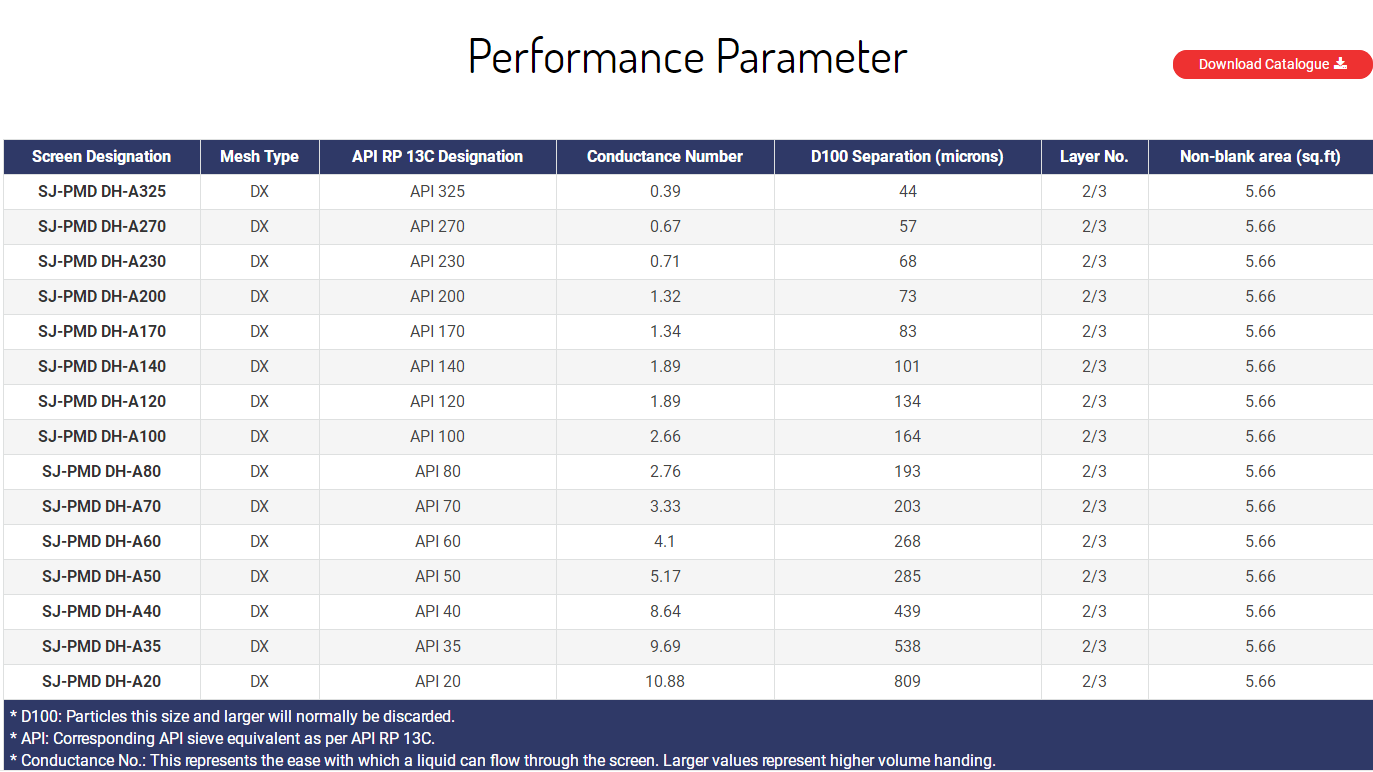
Remarks:
Derrick, Hyperpool, PMD, DX, DF, HP are marks of Derrick Corporation.
ShengJia only produces the replacement screens but not original from Derrick
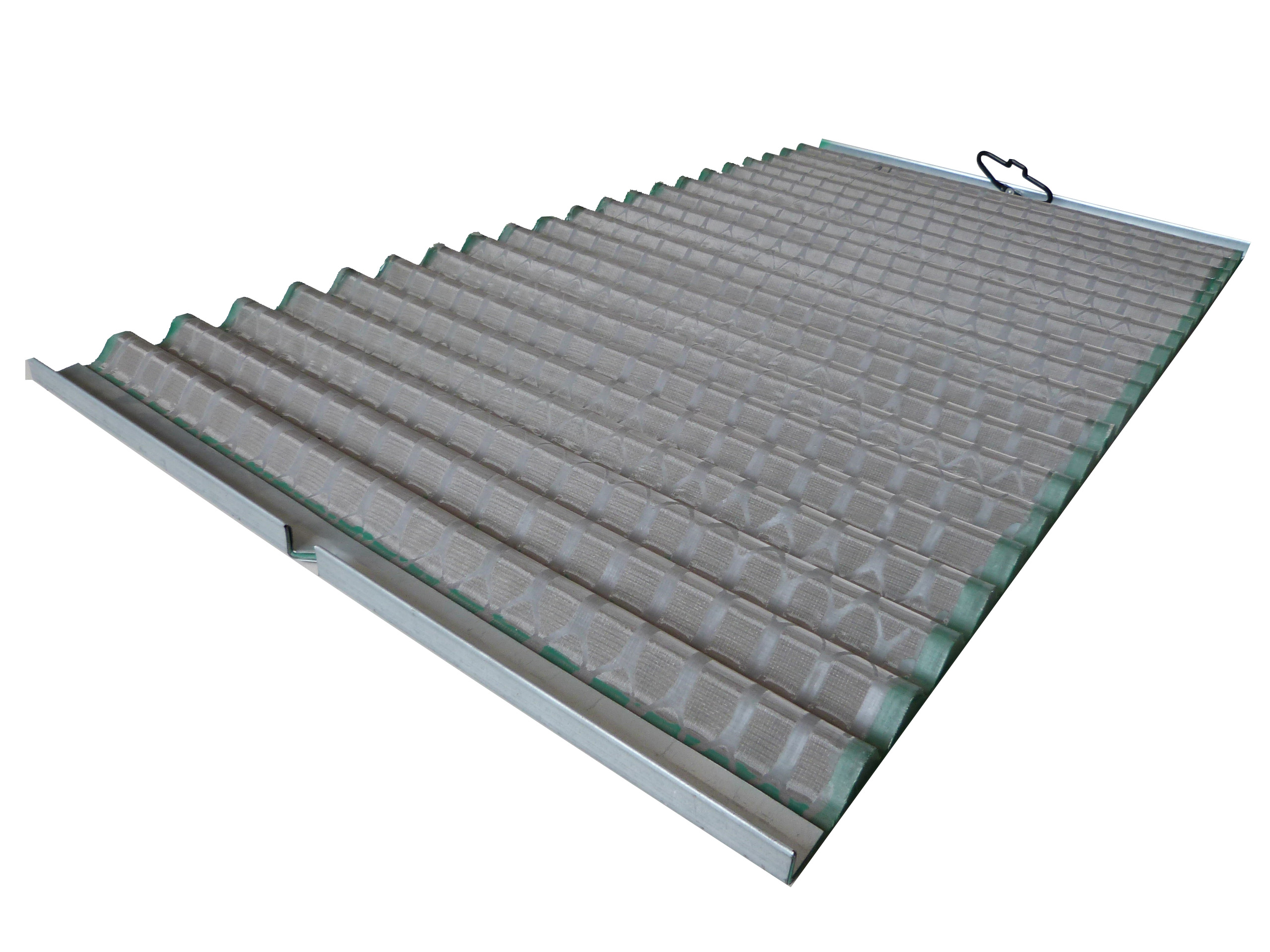
Derrick Hyperpool PMD Shaker Screen
Sieve Shaker Machine,Derrick Hyperpool Pwp Shaker Screen,Derrick Hyperpool Pyramid Shale Shaker Screen,Derrick Hyperpool Pmd Shaker Screen
Anping Shengjia Hardware Mesh Co.,ltd , https://www.oilshakerscreen.com